Fiber-reinforced calcium silicate board is made from inorganic mineral or cellulose fibers combined with calcium and silica as the main cementing materials. These materials undergo pulping, molding, and then a high-temperature, high-pressure curing process in saturated steam, which forms calcium silicate colloid that solidifies into durable boards.
So, how exactly is calcium silicate formed, and what role do the reinforcing fibers play in the board? Based on my experience, I will explain each aspect in detail below.
Formation Mechanism of Calcium Silicate
Calcium silicate is synthesized through a hydrothermal reaction between calcium and silica materials. The calcium source, typically lime (CaO), includes materials like lime, slaked lime, and calcium carbide slag. The silica source, primarily composed of SiOโ, includes diatomaceous earth, quartz powder, and fly ash.
In practice, calcium silicate board production often incorporates a small amount of cement to improve moldability and control. Most manufacturers now use a lime-cement blend, replacing part of the lime with cement for better production control. The hydrothermal reaction of calcium silicate in this lime-cement system is illustrated in Fig 1.
The reaction mechanism of calcium silicate, as shown in Figure 2, can be divided into three main stages:
Normal-Pressure Pre-Curing Stage: In this initial stage, cement reacts in water to form dicalcium silicate (CโS) and tricalcium silicate (CโS). Under ambient conditions, CโS hydrates to produce CโSHโ, while CโS hydrates to form highly alkaline hydrated calcium silicate (CโSHโ) and Ca(OH)โ, though these compounds generally do not react significantly with the silica material.
Autoclave Curing Stage: As temperature and pressure rise, the silica material begins to dissolve rapidly and reacts with Ca(OH)โ to form highly alkaline hydrated calcium silicate (CโSH(A)), consuming Ca(OH)โ in the process. At elevated temperatures, CโSH(A) is unstable and reacts with remaining SiOโ to convert into low-alkalinity hydrated calcium silicate (CโSH(B)), forming new crystals that continuously grow into stable tobermorite crystals (Cโ SโHโ ).
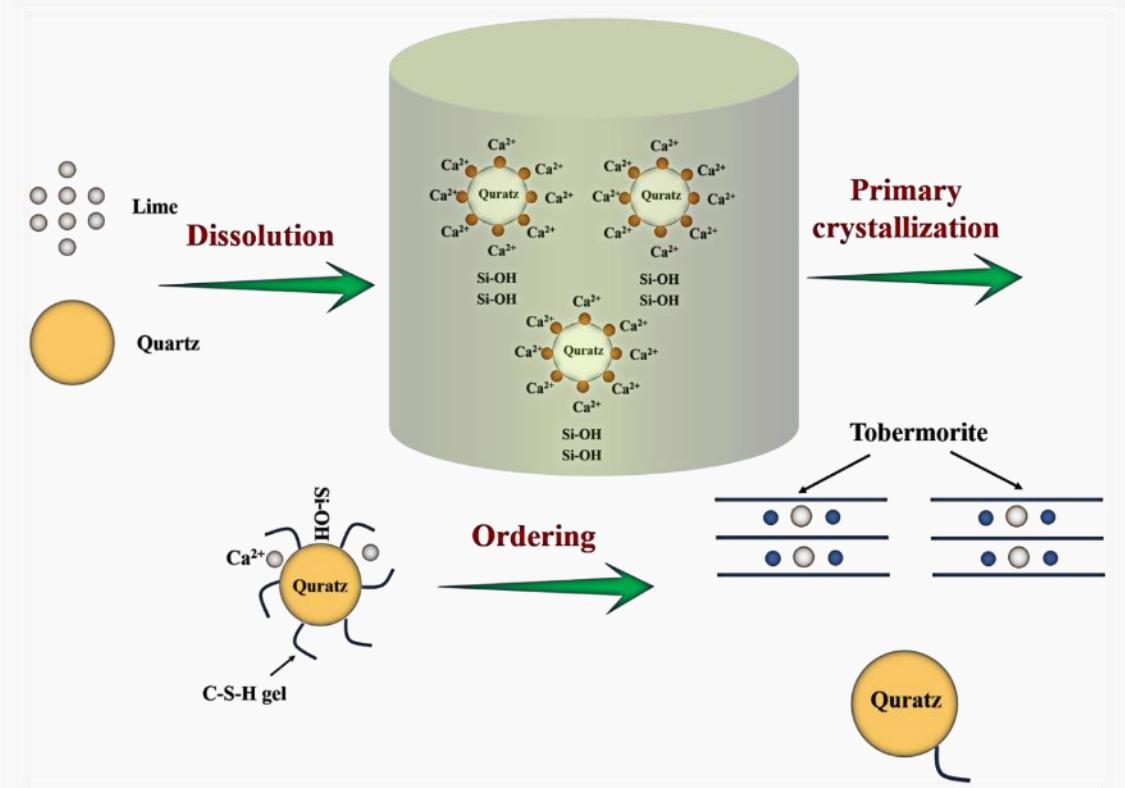
Extended Curing Stage: With prolonged autoclave curing, tobermorite crystals further react with SiOโ to produce xonotlite (CโSโH), a hard calcium silicate. Notably, due to the addition of cement, the reaction system becomes more complex. In actual hydrothermal synthesis, compounds such as calcium aluminate and gypsum from the water, as well as alumina from quartz sand, can result in a quaternary (CaO-SiOโ-AlโOโ-HโO) or even quinary (CaO-SiOโ-AlโOโ-CaSOโ-HโO) reaction system. Consequently, the final hydrothermal products are not just a simple mix of tobermorite and ettringite but may also include sodium silicate and other aluminum-containing calcium silicate hydrates. However, because of the stability and excellent crystalline structure of tobermorite, it remains the primary hydrate in calcium silicate boards, with some CโSH(B) allowed to ensure optimal physical and mechanical properties.
Differences Between Tobermorite and Xonotlite
Tobermorite and xonotlite are two primary types of calcium silicate hydrates with distinct properties. Xonotlite exhibits minimal shrinkage and the highest flexural strength among calcium silicate materials, though it requires higher synthesis temperatures and longer processing times compared to tobermorite and CSH(B).
Tobermorite products, typically synthesized via static hydrothermal methods, have limited heat resistance (up to 650ยฐC) and relatively high density, making them suitable mainly for the petrochemical industry.
Xonotlite products, on the other hand, are synthesized using dynamic hydrothermal methods, giving them excellent high-temperature resistance (up to 1000ยฐC) and low density. Xonotlite fibers are also bio-soluble, ensuring high safety standards. With these advantages, xonotlite is widely used in high-temperature industries, including metallurgy, chemical engineering, and construction materials. FireSafeโs fire-resistant board series exemplifies top-quality xonotlite-based calcium silicate boards.
Hard calcium silicate forms either as prismatic crystals or as fibrous aggregates aligned parallel to the b-axis. Under a chemical or electron microscope, synthetic hard calcium silicate crystals appear as flakes. The fibrous crystals have radii of several hundred nanometers and lengths reaching several thousand nanometers. Despite their fibrous structure, these crystals do not form voids with radii in the tens of microns; instead, they aggregate into hollow spherical structures. Many of these agglomerates reach diameters of tens of micrometers, forming voids with radii of 10-30 ฮผm. Larger spherical agglomerates create more substantial internal hollows and wider gaps between the aggregates, resulting in a lower bulk density as the agglomerate diameter increases.
The spherical agglomerate structure plays a crucial role in achieving the material’s ultra-low density. This material is typically formed by pressing and drying a slurry of hard calcium silicate. During the filter-pressing process, the fine fibrous crystals of calcium silicate are dispersed by water flow, reducing gaps between the crystals and increasing density due to capillary forces.
However, when these fibrous crystals form spherical agglomerates, water flow during filter-pressing cannot align them directionally. This provides the agglomerates with sufficient strength to resist over-compression. During drying, the large gaps between spheres accelerate water evaporation and prevent unrestricted fiber compaction, which reduces excessive capillary forces. This minimizes shrinkage and ensures the material remains ultra-light.
Mechanism and Performance Requirements of Fiber Reinforcement
Fiber materials enhance calcium silicate boards by blocking cracks, toughening the structure, and reducing the formation and spread of internal defects. The reinforcing effect depends on various factors, including fiber type, aspect ratio, pulping treatment, distribution, orientation, and the bonding strength between fibers and the board matrix.
A uniform fiber distribution forms an interconnected network within the board, maximizing reinforcement. In contrast, uneven distribution leads to two issues: fiber clumping, which causes density inconsistencies, increases water absorption, and shortens the board’s lifespan; and fiber-deficient areas, which are more susceptible to damage from external forces, compromising the boardโs integrity.
Fiber orientation affects board strength. If fibers are arranged directionally during molding, the board may exhibit a high strength disparity between longitudinal and transverse directions, reducing overall quality.
The bonding strength between the fiber and the matrix is crucial for durability. Studies show that the fiber-matrix interface is the most vulnerable part of the board. When fibers bond strongly with the matrix, they absorb more impact energy, significantly enhancing the boardโs toughness and strength. Randomly oriented fibers improve the board’s continuity and reduce internal defects, further reinforcing its structural integrity.
With the development of calcium silicate boards, the harmful effects of asbestos fibers, traditionally used as reinforcing materials, became evident. In response, many countries began regulating asbestos use in 1969. To address these challenges, researchers have increasingly explored alternative reinforcing fibers, such as plant fibers and glass fibers, which are now widely recognized to require the following properties:
Good Dispersion in Water: Fibers should disperse well in water, with a stable water film forming on their surface.
Alkaline Corrosion Resistance: Fibers must withstand alkaline solutions with a pH of 12-14, as the calcium silicate preparation process is highly alkaline, which can severely corrode fibers.
High Temperature and Pressure Resistance: Under hydrothermal conditions, fibers should maintain compatibility with the matrix, along with sufficient strength and toughness.
Fig.7 Plant Fiber and Glass Fiber
While fibers play a reinforcing role, there is an inherent trade-off between fiber content and product weight. Higher fiber content increases mechanical strength but also raises the weight of the product, reducing its thermal insulation properties. Conversely, low fiber content keeps the product ultralight but compromises its mechanical strength, potentially failing to meet performance standards. Additionally, fiber doping impacts production costs. Thus, determining an optimal fiber content is crucial to balance the mechanical strength and ultralight properties of hard calcium silicate materials.
Understanding the composition of calcium silicate boards provides insight into their durability, thermal resistance, and adaptability in various applications. From fiber reinforcement to careful control of material ratios, each component plays a crucial role in achieving the desired performance. If you have further questions or need additional information about calcium silicate boards, feel free to reach out to the experts at FireSafe.