Advances in technology have made building structures more sophisticated. However, this has created new challenges for fire safety. To address these issues, innovative fire-resistant materials have been introduced, providing essential support for building safety.
Among the most commonly used fireproof materials are calcium silicate boards and magnesium oxide boards. These materials compete in various applications, such as tunnel fire protection. In this article, we will compare calcium silicate boards and magnesium oxide boards from different perspectives, helping you determine which material is best suited for your specific needs.
What is a Magnesium Oxide Board?
Magnesium oxide board, also known as magnesium silicate panel, is a building material composed of magnesium oxide, magnesium cement gel, lightweight fillers (such as perlite and plant fibers), and an outer layer reinforced with fiberglass mesh.
Production Process
The production of magnesium oxide board generally involves three main steps:
Preparation๏ผRaw materials are measured in specific quantities and mixed into a slurry.
Forming and Conveying๏ผNon-woven fabric and fiberglass cloth are unrolled and fed into the molding machine. Molds are placed on standby on the machine platform, and the slurry from the mixer flows into the molds. The material is then extruded into the required magnesium board specifications, cut to the desired length, and sent to the curing room for maintenance.
Dehalogenation๏ผAfter demolding, the partially cured magnesium board is soaked in water for dehalogenation treatment, followed by a second round of curing.
Common Molding Methods
Currently, there are four main molding methods for magnesium oxide boards:
- Two or more layers of fiberglass cloth, one layer of pulp, and one layer of non-woven fabric (used in about 70% of production).
- A bottom layer of pulp, a surface layer of pulp, two or more layers of fiberglass cloth, and one layer of non-woven fabric.
- A bottom layer of pulp, a surface layer of pulp, an intermediate pulp layer, two or more layers of fiberglass cloth (without non-woven fabric).
- Similar to gypsum board production, without a central layer, with both sides wrapped in reinforcing materials.
Importance of Conservation for Magnesium Oxide Boards
Proper conservation of magnesium oxide boards is essential to ensure product stability and prevent deformation. Conservation is divided into primary and secondary stages:
- Primary Conservation: This is carried out with the mold still in place.
- Secondary Conservation: After demolding, the board undergoes additional maintenance.
Conservation Process
Conservation must adhere to the chemical reaction principles of magnesium materials. During molding, it is critical to maintain the product in an environment with the right temperature, humidity, and sufficient curing time to promote the chemical reaction:
5MgO+MgCl2โ+13H2โOโ5Mg(OH)2โโ 2MgCl2โโ 8H2โO
In this reaction, as much free MgClโ and water as possible are absorbed, leading to a hardened state. This reduces free water and results in a stable, dry product. This process ensures that the board achieves volume stability, minimizing deformation during use.
Common Issues in Conservation
To speed up production, some manufacturers use high-temperature heating for rapid surface hardening and early demolding. However, this can lead to:
Cracking and Deformation: High temperatures cause rapid moisture loss, leading to insufficient hardening and large amounts of free MgO and MgClโ. When exposed to moisture during use, the board may react again, creating internal stress and causing cracking.
Poor Volume Stability: Without proper conservation, free water remains inside, leading to shrinkage in dry conditions and generating internal stress.
These stresses can severely impact product integrity, often resulting in quality issues in construction applications.
The Issue of Halogenation
In addition to cracking and deformation, magnesium oxide boards face a challenge known as halogenation. Magnesium-based binders typically fall into two categories:
Magnesium Chloride (MgClโ): Magnesium chloride systems are less stable and absorb significant moisture from the air. In humid conditions, water may precipitate on the surface, causing reduced strength, deformation, and cracking, a process known as โhalogenation cracking.โ
Magnesium Sulfate (MgSOโ): To improve stability, MgSOโ-based binders are increasingly used as a replacement for MgClโ. While magnesium sulfate panels are less prone to moisture absorption, long-term exposure to high humidity can still cause water absorption, leading to weight gain, strength reduction, and corrosion of metal fixtures.
Researchers have analyzed magnesium sulfate-based magnesium plates using thermogravimetric analysis (TGA) to study mass loss as temperature increases. The TGA results, shown in the graph, indicate the following:
- At 600ยฐC: The plate exhibits a total mass loss of approximately 32%.
- At 1000ยฐC: The total mass loss increases to around 42%.
This data highlights the thermal stability of the magnesium sulfate-based plates and offers valuable insights into their behavior under high temperatures.
While the release of free and crystalline water during heating can absorb heat and contribute to fire resistance, the dehydration process can cause significant deformation and cracking in magnesium glass panels, leading to a loss of structural integrity. Although magnesium glass panels are classified as non-combustible, their fire resistance is limited:
Fire Resistance Tests: Cracking begins at 450ยฐC, with deformation, severe cracking, and eventual failure occurring at 750ยฐC.
Some magnesium glass panels are reinforced with flame-retardant polystyrene particles to improve insulation and reduce weight. Although flame-retardant polystyrene does not ignite, it decomposes under high temperatures, causing a rapid loss of strength and structural integrity. Consequently, using magnesium glass panels with polystyrene fillers in passive fireproofing structures or building components poses a significant safety risk.
Calcium Silicate Board
Calcium silicate board is a building material made from short reinforcing fibers (such as inorganic mineral fibers or cellulose fibers) and siliceous-calcium materials as the main cementing agents. Through a high-temperature, high-pressure steam curing process, calcium silicate gel is formed, creating a durable and heat-resistant board. For a more in-depth overview, please refer to our detailed article on What is Calcium Silicate Board?.
Types of Calcium Silicate Board
Calcium silicate boards can be categorized into Tobermorite Panels and Hard Calcium Silicate Panels, with each type having unique properties and applications:
Tobermorite Panels
- Properties: Manufactured via static hydrothermal synthesis, these panels are generally heavier and have moderate heat resistance, with a maximum temperature tolerance of up to 650ยฐC.
- Applications: Primarily used in lower-temperature environments within the petrochemical industry.
Hard Calcium Silicate Panels
- Properties: Produced through dynamic hydrothermal synthesis, these panels exhibit high-temperature stability (up to 1000ยฐC) and low density. Hard calcium silicate offers minimal shrinkage and exceptional flexural strength, making it highly stable. Its fibers are also biocompatible, enhancing safety for widespread industrial use.
- Applications: Commonly used in high-temperature industries such as metallurgy, chemical processing, and construction materials, especially for high-temperature insulation in pipelines and furnace linings.
Key Differences
Attribute | Tobermorite Panels | Hard Calcium Silicate Panels |
---|---|---|
Maximum Temperature
|
650ยฐC
|
1000ยฐC
|
Manufacturing Method
|
Static Hydrothermal Process
|
Dynamic Hydrothermal Process
|
Density
|
Higher
|
Lower
|
Typical Applications
|
Petrochemical, low-temperature uses
|
Metallurgy, chemical processing, high-temp applications
|
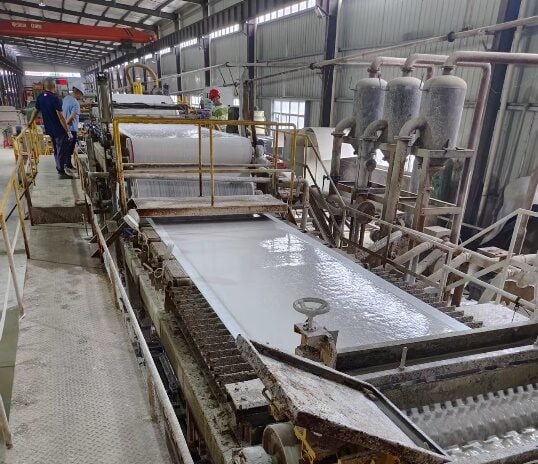
Importance of Autoclave Curing in Calcium Silicate Board Production
Similar to magnesium oxide boards, the steaming or autoclaving process is a critical step in the production of calcium silicate boards. During autoclaving, siliceous and calcareous materials undergo continuous hydrothermal synthesis, forming an interconnected crystalline structure that bonds tightly with reinforcing fibers. This process gives calcium silicate boards their strength but can also lead to structural defects, including internal pressure build-up, reduced mechanical properties, and cracking, especially along board edges. These issues can be addressed during the maintenance phase.
FireSafeโs Solution
FireSafe focuses on producing low-density, fire-resistant calcium silicate boards that offer a balance of lightweight construction, strength, and competitive pricing as an alternative to Promat products. Our product range is designed to meet various fire protection requirements in both industrial and commercial applications.
Application
The following graph presents the results of a 90-minute fire resistance test conducted on 8 mm thick magnesium oxide and calcium silicate boards by a Chinese fire protection supplier, using the ASTM E119 method.
Calcium Silicate Board: Displayed only minor deformation.
Magnesium Oxide Board: Exhibited significant chalking, with the internal glass fiber network exposed, resulting in a complete loss of insulation.
In addition to limited fire resistance, the ongoing halogenation issue of magnesium oxide boards further restricts their use. The China Building Materials Federation issued an advisory to Shanghai contractors, explicitly stating that magnesium oxide boards are unsuitable for use in wet tunnel environments.
Furthermore, Beijingโs “Announcement of the Second Catalogue of Products for the Restriction and Elimination of Outdated Building Materials” prohibits the use of magnesium oxide boards in indoor insulation projects for all types of buildings since 2000.
The Hong Kong Highways Department (HyD) explicitly prohibits the use of MgO panels in tunnel projects, as stated in clause 2.6.3 of the โDesign Guidelines for Road Tunnel Structures and Tunnel Buildings.โ
The UKโs leading building industry organization, the Window and External Cladding Association, has highlighted the common corrosion issues associated with magnesium silicate panels. Similar issues have also been reported in Denmark, Canada, and Australia.
The Canadian Union of Building Officials’ Associations (CUBOA), an affiliate of the Government of Canada, has acknowledged the issues associated with magnesium silicate panels reported in Denmark, China, and Australia. CUBOA recommends suspending the use of these panels until the CCMC reaches a consensus conclusion.
The NHBC, the UKโs oldest provider of warranties and insurance for new homes, and LABC, another leading insurance provider, have declined to offer coverage for magnesium silicate panels.
Conclusion
Magnesium oxide boards offer benefits such as being lightweight, flexible, and easy to process. However, due to unresolved halogenation issues, they are not recommended for use in wet environments. For moisture-sensitive applications, such as tunnels, calcium silicate boards provide a safer and more dependable option.
With over 12 years of experience in passive fire protection, my team and I have assisted more than 100 clientsโincluding wholesalers, contractors, and buildersโin finding the right solutions for their projects. If you have any questions or would like more information, please feel free to contact us for a free, no-obligation quote or to discuss a solution tailored to your needs.