Kalziumsilikatplatte besteht aus anorganischen Mineralfasern oder Zellulosefasern, kombiniert mit anderen losen Kurzfasern als Verstärkungsmaterial. Kieselsäure und Kalziumverbindungen dienen als primäre Bindemittel. Das Herstellungsverfahren umfasst Aufschluss, Formgebung und eine beschleunigte Aushärtungsreaktion unter gesättigtem Dampf bei hoher Temperatur und hohem Druck, wodurch eine dauerhafte Kalziumsilikatplatte entsteht.
Durch Anpassung des Rohstoffverhältnisses und der Produktionsverfahren, Kalziumsilikatplatten mit unterschiedlichen Eigenschaften hergestellt werden, um verschiedenen Anwendungsanforderungen gerecht zu werden. Diese Anpassungsfähigkeit gewährleistet die Eignung des Materials für unterschiedliche Arbeitsbedingungen. Wie genau wird eine Kalziumsilikatplatte hergestellt, und wie beeinflussen die Produktionsmethoden ihre Leistung?
Verfahren zur Herstellung von Kalziumsilikatplatten
Nach jahrzehntelanger Entwicklung ist der Produktionsprozess für Kalziumsilikatplatten standardisiert und rationalisiert worden. Zu den wichtigsten Schritten gehören die Aufbereitung des Rohmaterials, der Aufschluss, das Formen der Platten, die Aushärtung im Autoklaven und die Nachbehandlung. Hier finden Sie einen Überblick über den Prozess:
Vorbereitung des Rohmaterials
Diese Phase umfasst:
Quarzsand Nassschleifen: Zur Erzielung der für den Aufschluss erforderlichen Feinheit.
Branntkalk-Löschung: Sorgt für optimale Reaktivität.
Verarbeitung von Fasermaterial: Schleifen und Dispergieren von Fasern zur Verbesserung der Gleichmäßigkeit.
Zellstoffherstellung
Faserzellstoff wird in einem Gegenstrommischer mit Materialien auf Kalzium- und Kieselsäurebasis vermischt, um eine gleichmäßige Dispersion zu erreichen. Die Mischung wird in einen Brei mit gleichmäßiger Konzentration umgewandelt, der in einem Zellstofftank gelagert wird. Einige Hersteller verarbeiten den Brei mit Hilfe von Mühlen weiter, um eine gleichmäßige Vermischung von Fasern und Partikeln zu gewährleisten.
Blechformung
Der Schlamm wird auf ein Förderband verteilt und entwässert, um dünne Schichten von Rohlingen zu bilden. Diese Lagen werden bis zur gewünschten Dicke um einen Formzylinder gewickelt. Sobald die Bramme die vorgegebenen Abmessungen erreicht hat, wird sie von einem automatischen Schneidesystem zugeschnitten, und die Brammen werden gestapelt und gepresst, um die Festigkeit und Kompaktheit zu erhöhen.
Aushärtung im Autoklaven
Die Platten werden in einen Autoklaven gelegt, wo sie eine chemische Reaktion mit Kieselsäure, Kalziumhydroxid und Wasser eingehen. Bei dieser Reaktion bilden sich Tobermoritkristalle und hartes Kalziumsilikat, die für die Festigkeit, Dimensionsstabilität und Feuchtigkeitsbeständigkeit der Platte unerlässlich sind.
Trocknung und Nachbehandlung
Nach dem Aushärten werden die Platten getrocknet, um den Standardfeuchtigkeitsgehalt zu erreichen. Abschließende Qualitätskontrollen gewährleisten, dass nur konforme Produkte als fertige Kalziumsilikatplatten geliefert werden.
In diesem Prozess, Blechformteil und Autoklavenhärtung sind besonders kritisch für die Qualität des Endprodukts. Diese Stufen haben einen direkten Einfluss auf die Festigkeit, die Ausdehnungsrate und die Feuchtigkeitsbeständigkeit des Kartons und sind daher die Hauptpunkte für die weitere Prozessoptimierung.
Die folgenden Abschnitte befassen sich mit diesen beiden Prozessendie ihren Einfluss auf die Leistung von Kalziumsilikatplatten deutlich machen.
Stanz- und Formgebungsverfahren
Nach der Aufschlussphase wird der gemischte Schlamm verteilt, entwässert und durch Strangpressen zu Kalziumsilikatplatten-Rohlingen geformt. Das Stanzverfahren wird hauptsächlich in zwei Methoden unterteilt, wobei die Methode des Kopierens ist eine der am häufigsten verwendeten Methoden.
Methode des Kopierens
Das Kopierverfahren, eine Art Nassverfahren, wurde erstmals Anfang des 20. Jahrhunderts von Hatschek zur Herstellung von Faserzementverbundwerkstoffen eingeführt. Im Laufe der Jahre wurde dieses Verfahren verfeinert und ist nach wie vor ein wichtiger Ansatz bei der Herstellung von Kalziumsilikatplatten.
Das Layout der Produktionslinie für das Kopierverfahren umfasst drei Hauptabschnitte:
Sektion Zellstofferzeugung: Bereitet die Gülle vor.
Mesh Box Abschnitt: Bildet die leeren Ebenen.
Blanko Verarbeitung Abschnitt: Verarbeitet die Rohlinge zu fertigen Produkten.
Wie in Abb. 4beginnt der Kopiervorgang mit dem Netzradmechanismusdie den aufbereiteten Zellstoff auf ein Industrietuch überträgt. Das Gummituch transportiert den Zellstoff zu den Entwässerungs- und Extrusionsformabschnitten. Der Zylinder der Formmaschine komprimiert und verdichtet die Rohlinge. Wenn sich das Gummituch vom Formzylinder löst, entsteht ein Unterdruck zwischen dem Rohling und der Zylinderoberfläche, so dass der Rohling fest am Formzylinder haftet. Sobald die gewünschte Dicke erreicht ist, wird der Rohling geschnitten und zur nächsten Produktionsstufe transportiert.
Vorteile und Beschränkungen
Beim Kopierverfahren werden Kalziumsilikatplatten mit:
Gleichmäßige Schichtverteilung: Gewährleistet eine gleichbleibende Materialqualität.
Hohe Festigkeit und Ebenheit: Bietet eine hervorragende strukturelle Integrität und eine glatte Oberfläche.
Diese Methode erfordert jedoch eine große Produktionsfläche, ist energieintensiv und erfordert eine komplexe Wartung.
Fließzellstoff-Methode
Das Fließzellstoffverfahren gehört wie das Kopierverfahren zur Kategorie der Nassverfahren. Während der gesamte Produktionsprozess dem Kopierverfahren weitgehend ähnelt, liegt der Hauptunterschied in der Art und Weise, wie der Zellstoff verteilt wird. Anstelle eines Netzrads für den Stofftransport stützt sich das Fließbandverfahren auf einen Fließbandkasten als Kernmechanismus.
Bei diesem Verfahren wird der vorgemischte Schlamm in den Zellstoffkasten gepumpt, der ihn gleichmäßig auf ein industrielles Drucktuch aufträgt. Das Gummituch transportiert den Schlamm dann durch mehrere Vakuumentwässerungskästen, bevor er zur Extrusion, Dehydrierung und Formung in die Kalziumsilikatplattenformmaschine befördert wird.
Einer der Vorteile des Fließzellstoffkastens ist seine Fähigkeit, eine gleichmäßige Fließgeschwindigkeit über die gesamte Breite des Gummituchs aufrechtzuerhalten, was eine seitliche Strömung verhindert und eine gleichmäßige Verteilung des Schlamms gewährleistet. Dies führt zu einer gleichmäßigen Schlichtegeschwindigkeit über die gesamte Breite des Gummituchs, ohne Schwankungen.
Das Prozessdiagramm für die Fließpulp-Methode ist dargestellt in Abbildung 6.
Der hohe Feuchtigkeitsgehalt des Schlamms, der aus dem Stoffstromkasten auf das Industrietuch fließt, erfordert eine erhöhte Anzahl von Vakuumentwässerungssaugern in der Produktionslinie. Dies kann zu einer geringfügig geringeren Ebenheit und Festigkeit des Produkts führen. Im Vergleich zum Kopierverfahren benötigt das Fließschnitzelverfahren jedoch weniger Platz und verbraucht relativ weniger Energie.
Vergleich mit der Kopiermethode
Es ist wichtig zu beachten, dass die Fließzellstoff- und Kopierverfahren nicht austauschbar sind. Die Wahl des Verfahrens hängt von den Leistungsanforderungen an das Endprodukt und seinen Anwendungsszenarien ab. Nachstehend finden Sie einen detaillierten Vergleich:
Aspekt | Fließzellstoff-Methode | Methode des Kopierens |
---|---|---|
Prozess-Typ
|
Nasses Verfahren
|
Nasses Verfahren
|
Schichtdicke
|
Dickere Einzelschichten, weniger Gesamtschichten
|
Dünnere Einzelschichten, mehr Gesamtschichten
|
Anordnung der Fasern
|
Senkrechte Fasern bilden eine 3D-Verstärkungsstruktur
|
Ausrichtung der Fasern entlang der Bahnrichtung
|
Biegefestigkeit
|
Etwas niedriger
|
Höher
|
Druck-/Zugfestigkeit
|
Etwas höher
|
Unter
|
Energieverbrauch
|
Unter
|
Höher
|
Platzbedarf
|
Kleiner
|
Größere
|
Ebenheit der fertigen Platte
|
Geringfügig reduziert
|
Hoch
|
Schlüsselfaktoren, die die Qualität des Vorstands beeinflussen
Unabhängig von der Produktionsmethode spielt der Autoklavierungsprozess eine zentrale Rolle. In dieser Phase verwandeln sich die Kieselsäure- und Kalziumbestandteile in der Platte in chemisch stabile Tobermoritkristalle und hartes Kalziumsilikat. Der Kristallgehalt entscheidet direkt über die Qualität der fertigen Platte.
Faktor | Auswirkungen auf die Qualität |
---|---|
Anteil des Rohmaterials
|
Beeinflusst die Bildung von Tobermorit und harten Kalziumsilikatkristallen.
|
Verfahren zur Herstellung von Knüppeln
|
Beeinträchtigt die strukturelle Integrität und Gleichmäßigkeit der Rohlinge.
|
Autoklavierverfahren
|
Bestimmt die Stabilität, die Ausdehnungsrate und die Feuchtigkeitsbeständigkeit der Platten.
|
Durch die Feinabstimmung dieser Variablen können die Hersteller Folgendes produzieren Kalziumsilikatplatten die auf spezifische Anwendungsanforderungen zugeschnitten sind und ein optimales Gleichgewicht zwischen Leistung und Effizienz gewährleisten.
Dampfkompressionsverfahren
Hydrothermale Synthesemethode
Bei der Herstellung von Kalziumsilikatplatten werden Kalziumsilikatkristalle durch ein hydrothermales Verfahren in einem Hochtemperatur-Hochdruck-Autoklaven synthetisiert. Bei diesem Prozess, der als "Autoklav-Wartung" bezeichnet wird, reagieren Silizium- und Kalziummaterialien bei 180-200°C und 1-1,5 MPa für 13-20 Stunden um stabile Kristalle zu erzeugen.
Bei der hydrothermalen Synthesemethode wird Wasser als Medium für Reaktionen in einem chemischen Umfeld in flüssiger Phase verwendet. Je nachdem, ob gerührt wird oder nicht, wird die Methode in zwei Typen unterteilt: statisch und dynamisch.
Statische Methode:
Bei diesem Verfahren werden die Rohstoffe gemischt, zu nassen Platten geformt und vor der Autoklavstufe vorkonditioniert. Der Vorkonditionierungsprozess umfasst in der Regel Folgendes:
Temperatur: 50-70°C
Dauer: 4-5 Stunden
Sobald die Bramme eine ausreichende Festigkeit erreicht hat, wird sie entformt und für die hydrothermale Reaktion in den Autoklaven geschickt.
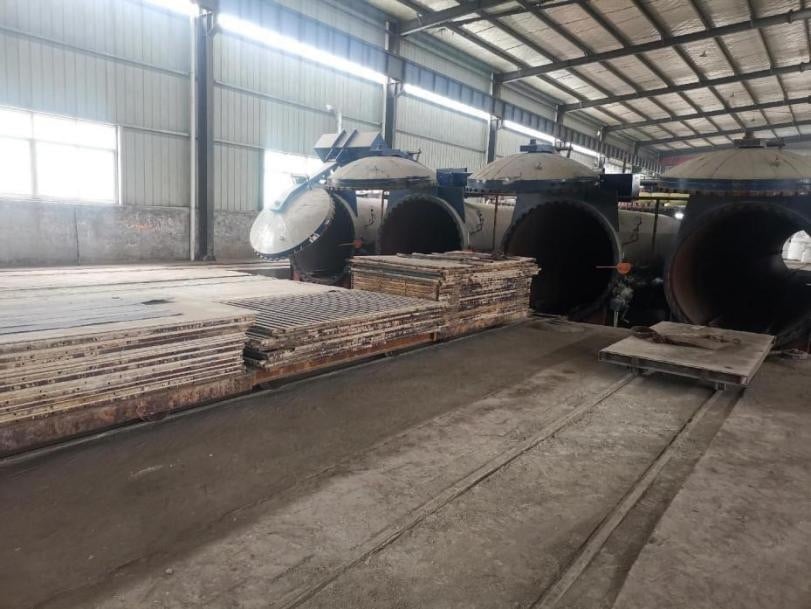
Dynamische Methode:
Bei dieser Methode werden die Rohstoffe während der Reaktion im Autoklaven gerührt. Durch das ständige Rühren bleiben die festen Partikel in der flüssigen Phase in der Schwebe, was ein gleichmäßiges Kristallwachstum und eine gleichmäßige Dispersion fördert. Es erleichtert auch die Bildung von harten Kalziumsilikatfasern mit großem Durchmesser. Diese Fasern neigen dazu, sich zu verflechten, wodurch hohle Sekundärteilchen entstehen, die zur Bildung von Kristallen beitragen:
Hohe Porosität: Verbessert die Wärmedämmung.
Niedrige Wärmeleitfähigkeit: Verbessert die Energieeffizienz.
Aspekt | Statische Methode | Dynamische Methode |
---|---|---|
Prozess
|
Stationäre hydrothermale Reaktion nach Vorkonditionierung.
|
Die Reaktion erfolgt unter ständigem Rühren.
|
Kristallwachstum
|
Erzeugt kleinere, weniger einheitliche Kristalle.
|
Fördert größere, gleichmäßig verteilte Kristalle.
|
Wärmedämmung
|
Mäßig
|
Hoch aufgrund erhöhter Porosität und Faserverflechtung.
|
Ausstattung Kosten
|
Geringere Investitionen.
|
Höhere Investitionen aufgrund der komplexen Ausrüstung.
|
Die dynamische Methode bietet aufgrund seiner Fähigkeit, hochporöse Strukturen zu bilden, hervorragende Wärmedämmeigenschaften, erfordert aber modernere Anlagen und höhere Kosten. Im Gegensatz dazu ist die statische Methode ist einfacher und kostengünstiger und eignet sich daher für Projekte mit Standardisolierungsanforderungen.
Typische Probleme und Lösungen im Verdampfungsprozess
Viele Experten sind sich einig, dass neben der Rezeptur die Kontrolle des Autoklavierprozesses ein Schlüsselfaktor für die Leistung von Kalziumsilikatplatten ist. Der Verdampfungsprozess beinhaltet die kontinuierliche hydrothermale Synthese von silikatischen und kalkhaltigen Materialien. Während dieses Prozesses bilden sich neue Kristalle und bestehende Kristalle wachsen, so dass schließlich kristalline Konidien mit einer räumlichen Struktur entstehen, die sich fest mit den Fasern verbinden und der Platte Festigkeit verleihen.
Bei diesem Verfahren können jedoch auch strukturelle Mängel auftreten, die die Festigkeit und andere physikalische Eigenschaften des Kartons verringern. Diese Defekte äußern sich vor allem in den folgenden Punkten:
1. Innendruck und strukturelle Lockerheit
Wenn sich die Platte während der Verdampfung erwärmt, dehnen sich das Wasser und die Luft in den inneren Poren aus und erzeugen einen Innendruck. In einem bestimmten Stadium kann dieser Innendruck den äußeren Dampfdruck übersteigen.
In der Zwischenzeit führt das fortgesetzte Wachstum der Kristalle zu Vergröberungwo sich größere Kristalle bilden. Dadurch verringert sich die Anzahl der Bindungspunkte zwischen den Kristallen, wodurch die kristalline Verbindung geschwächt wird und die Festigkeit abnimmt. Zusätzlich schwächen die inneren Zugspannungen durch den Kristallisationsdruck die Struktur weiter. Diese kombinierten Effekte können zu strukturellen Lockerungen und zur Bildung von Blasen und anderen Defekten in der Platte führen.
2.Board Edge Cracking
Rissbildung an den Plattenkanten ist ein bedeutender Herstellungsfehler, der die strukturelle Integrität von Kalziumsilikatplatten beeinträchtigen kann. Die Risse treten in der Regel entlang der Kanten auf, durchdringen die gesamte Plattendicke und reichen von einigen Zentimetern bis zu mehreren Zentimetern nach innen. Dieses Problem ist in erster Linie auf Temperatur- und Feuchtigkeitsunterschiede während der Dekompressionsphase zurückzuführen. Wenn die Temperatur an den Kanten unter die Innentemperatur sinkt, entstehen zerstörerische Spannungsmuster, die zu Rissen führen.
3. der Verlust der Faserstärke
Der Verlust der Faserfestigkeit ist eine der größten Herausforderungen bei der Herstellung von Kalziumsilikatplatten. Während der Übergang von Asbest zu Pflanzen- oder Glasfasern gesundheitliche Bedenken ausräumt, stellen diese alternativen Materialien beim Autoklavieren eine Herausforderung dar. Obwohl das Autoklavieren für die Bildung von Kalziumsilikathydratbindungen, die die Biegefestigkeit verbessern, unerlässlich ist, kann eine längere Exposition gegenüber hohen Temperaturen und alkalischen Bedingungen die Faserintegrität mit der Zeit beeinträchtigen.
Optimierung von Fertigungsprozessen
Um diesen Herausforderungen wirksam zu begegnen, sollten die Hersteller einen umfassenden Drei-Phasen-Ansatz verfolgen:
Vorkonditionierungsphase
Die Durchführung eines statischen Stopp- oder Trockenhitze-Vorkonditionierungsprozesses ist ein entscheidender vorbereitender Schritt. Dadurch wird die innere Feuchtigkeit reduziert, die druckbedingte Belastung während des Autoklavierens minimiert und die strukturelle Festigkeit des Kartons verbessert.
Druckmanagement
Eine genaue Kontrolle des Druckabbaus, insbesondere in den letzten Phasen der Druckbeaufschlagung, ist von entscheidender Bedeutung. Vorzeitige Druckänderungen können die strukturelle Integrität der Platte beeinträchtigen, bevor sie ihre optimale Festigkeit erreicht.
Kontrollierter Aushärtungsprozess
Um Temperatur- und Feuchtigkeitsbelastungen abzumildern, sollte ein sanftes Knickverfahren angewendet werden. Der Prozess sollte so kalibriert werden, dass eine moderate Tobermoritbildung im Hydrid gefördert wird, wobei eine erweiterte hydrothermale Behandlung Platten vorbehalten ist, die verbesserte Eigenschaften erfordern.
Der Firesafe-Ansatz
Als Branchenführer in der Herstellung von Kalziumsilikatplatten, Firesafe hat firmeneigene Verfahren entwickelt, um diese Herausforderungen umfassend zu bewältigen. Durch fortschrittliche Faserkonservierungstechniken und strenge Qualitätskontrollmaßnahmen liefert Firesafe durchgängig Kalziumsilikat-Brandschutzplatten, die die Branchenstandards für strukturelle Integrität und Leistung übertreffen.