Faserverstärkte Kalziumsilikatplatten werden aus anorganischen Mineral- oder Zellulosefasern in Kombination mit Kalzium und Siliziumdioxid als den wichtigsten Bindemitteln hergestellt. Diese Materialien werden zerkleinert, geformt und anschließend bei hohen Temperaturen und unter hohem Druck in gesättigtem Wasserdampf ausgehärtet, wodurch ein Kalziumsilikatkolloid entsteht, das sich zu dauerhaften Platten verfestigt.
Wie genau entsteht also Kalziumsilikat, und welche Rolle spielen die Verstärkungsfasern in der Platte? Ausgehend von meiner Erfahrung werde ich im Folgenden jeden Aspekt im Detail erläutern.
Entstehungsmechanismus von Calciumsilikat
Calciumsilicat wird durch eine hydrothermale Reaktion zwischen Calcium und Siliciumdioxid synthetisiert. Die Calciumquelle, in der Regel Kalk (CaO), umfasst Materialien wie Kalk, gelöschten Kalk und Calciumcarbidschlacke. Die Kieselsäurequelle, die hauptsächlich aus SiO₂ besteht, umfasst Diatomeenerde, Quarzpulver und Flugasche.
In der Praxis wird bei der Herstellung von Kalziumsilikatplatten oft eine geringe Menge Zement zugesetzt, um die Formbarkeit und die Kontrolle zu verbessern. Die meisten Hersteller verwenden heute eine Kalk-Zement-Mischung, bei der ein Teil des Kalkes durch Zement ersetzt wird, um die Produktion besser kontrollieren zu können. Die hydrothermale Reaktion von Calciumsilicat in diesem Kalk-Zement-System ist in Abb. 1 dargestellt.
Der in Abbildung 2 dargestellte Reaktionsmechanismus von Kalziumsilikat lässt sich in drei Hauptphasen unterteilen:
Vorhärtungsphase bei Normaldruck: In diesem Anfangsstadium reagiert Zement in Wasser zu Dicalciumsilikat (C₂S) und Tricalciumsilikat (C₃S). Unter Umgebungsbedingungen hydratisiert C₂S zu C₂SH₂, während C₃S zu stark alkalischem hydratisiertem Kalziumsilikat (C₂SH₂) und Ca(OH)₂ hydratisiert, obwohl diese Verbindungen im Allgemeinen nicht nennenswert mit dem Siliziumdioxidmaterial reagieren.
Autoklave Aushärtungsstufe: Mit steigender Temperatur und steigendem Druck beginnt sich das Siliziumdioxidmaterial schnell aufzulösen und reagiert mit Ca(OH)₂ zu hochalkalischem hydratisiertem Kalziumsilikat (C₂SH(A)), wobei Ca(OH)₂ verbraucht wird. Bei höheren Temperaturen ist C₂SH(A) instabil und reagiert mit dem verbleibenden SiO₂ zu hydratisiertem Kalziumsilikat mit geringer Alkalität (C₂SH(B)) und bildet neue Kristalle, die kontinuierlich zu stabilen Tobermoritkristallen (C₅S₆H₅) heranwachsen.
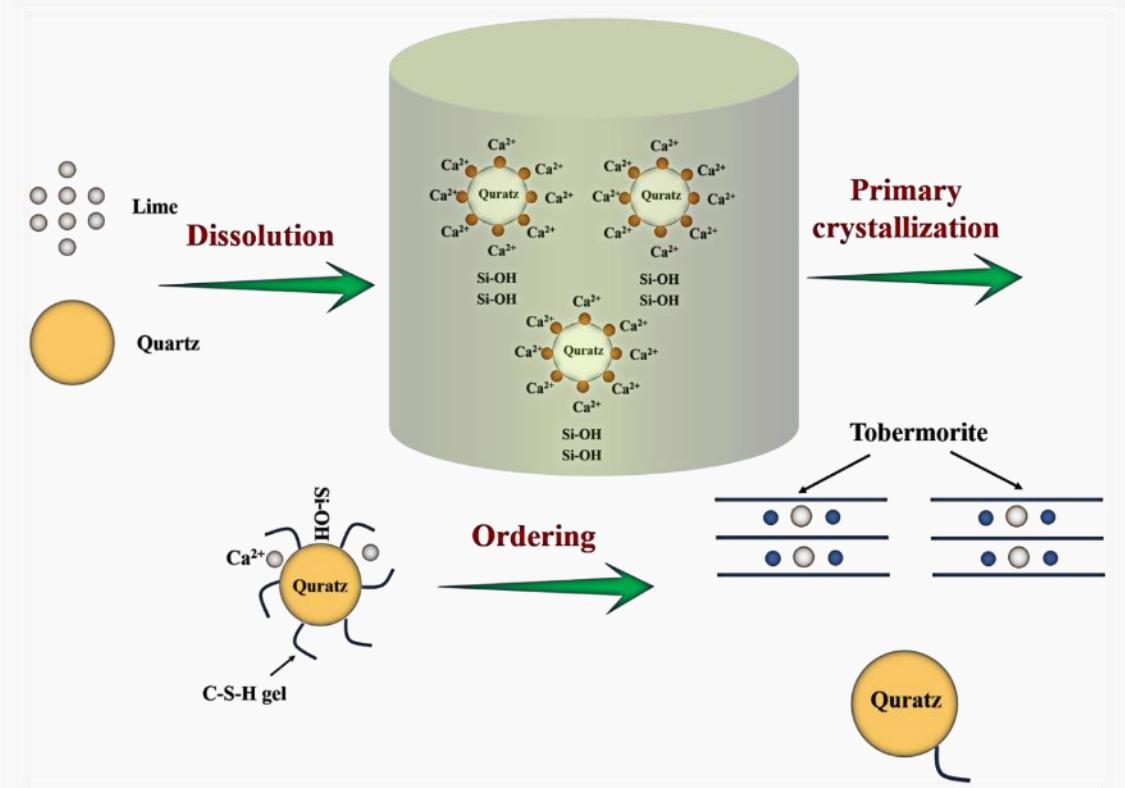
Erweiterte Aushärtungsphase: Bei längerer Aushärtung im Autoklaven reagieren die Tobermoritkristalle weiter mit SiO₂ zu Xonotlit (C₆S₆H), einem harten Calciumsilikat. Durch die Zugabe von Zement wird das Reaktionssystem noch komplexer. Bei der hydrothermalen Synthese können Verbindungen wie Calciumaluminat und Gips aus dem Wasser sowie Tonerde aus Quarzsand zu einem quaternären (CaO-SiO₂-Al₂O₃-H₂O) oder sogar quinären (CaO-SiO₂-Al₂O₃-CaSO₄-H₂O) Reaktionssystem führen. Folglich sind die hydrothermalen Endprodukte nicht nur eine einfache Mischung aus Tobermorit und Ettringit, sondern können auch Natriumsilikat und andere aluminiumhaltige Calciumsilikathydrate enthalten. Aufgrund der Stabilität und der ausgezeichneten kristallinen Struktur von Tobermorit bleibt es jedoch das wichtigste Hydrat in Kalziumsilikatplatten, wobei ein gewisser Anteil an C₂SH(B) zulässig ist, um optimale physikalische und mechanische Eigenschaften zu gewährleisten.
Unterschiede zwischen Tobermorit und Xonotlit
Tobermorit und Xonotlit sind zwei Haupttypen von Calciumsilikathydraten mit unterschiedlichen Eigenschaften. Xonotlit weist eine minimale Schrumpfung und die höchste Biegefestigkeit unter den Kalziumsilikaten auf, erfordert jedoch im Vergleich zu Tobermorit und CSH(B) höhere Synthesetemperaturen und längere Verarbeitungszeiten.
Tobermoritprodukte, die in der Regel durch statische hydrothermale Verfahren synthetisiert werden, weisen eine begrenzte Hitzebeständigkeit (bis zu 650 °C) und eine relativ hohe Dichte auf und eignen sich daher hauptsächlich für die petrochemische Industrie.
Xonotlite-Produkte hingegen werden mit dynamischen hydrothermalen Verfahren synthetisiert, was ihnen eine ausgezeichnete Hochtemperaturbeständigkeit (bis zu 1000 °C) und eine geringe Dichte verleiht. Xonotlite-Fasern sind außerdem biolöslich und gewährleisten hohe Sicherheitsstandards. Aufgrund dieser Vorteile wird Xonotlite häufig in der Hochtemperaturindustrie eingesetzt, z. B. in der Metallurgie, der Chemietechnik und bei Baumaterialien. Die feuerfeste Plattenserie von FireSafe ist ein Beispiel für qualitativ hochwertige Kalziumsilikatplatten auf Xonotlitbasis.
Hartes Kalziumsilikat bildet sich entweder als prismatische Kristalle oder als faserige Aggregate, die parallel zur b-Achse ausgerichtet sind. Unter dem Chemie- oder Elektronenmikroskop erscheinen synthetische Kalziumhartsilikatkristalle als Flocken. Die faserigen Kristalle haben Radien von mehreren hundert Nanometern und Längen von mehreren tausend Nanometern. Trotz ihrer faserigen Struktur bilden diese Kristalle keine Hohlräume mit Radien im zweistelligen Mikrometerbereich; stattdessen aggregieren sie zu hohlen kugelförmigen Strukturen. Viele dieser Agglomerate erreichen Durchmesser von zehn Mikrometern und bilden Hohlräume mit Radien von 10-30 μm. Größere kugelförmige Agglomerate erzeugen größere innere Hohlräume und breitere Lücken zwischen den Aggregaten, was zu einer geringeren Schüttdichte führt, wenn der Agglomeratdurchmesser zunimmt.
Die kugelförmige Agglomeratstruktur spielt eine entscheidende Rolle beim Erreichen der extrem niedrigen Dichte des Materials. Dieses Material wird in der Regel durch Pressen und Trocknen einer Aufschlämmung von hartem Kalziumsilikat hergestellt. Während des Filterpressens werden die feinen faserigen Kalziumsilikatkristalle durch den Wasserfluss dispergiert, wodurch sich die Lücken zwischen den Kristallen verringern und die Dichte aufgrund von Kapillarkräften erhöht.
Wenn diese Faserkristalle jedoch kugelförmige Agglomerate bilden, kann der Wasserfluss beim Pressen des Filters sie nicht ausrichten. Dadurch erhalten die Agglomerate eine ausreichende Festigkeit, um einer Überkomprimierung zu widerstehen. Während des Trocknens beschleunigen die großen Lücken zwischen den Kugeln die Wasserverdunstung und verhindern eine ungehinderte Verdichtung der Fasern, wodurch übermäßige Kapillarkräfte reduziert werden. Dies minimiert die Schrumpfung und sorgt dafür, dass das Material ultraleicht bleibt.
Mechanismus und Leistungsanforderungen der Faserbewehrung
Fasermaterialien verbessern Kalziumsilikatplatten, indem sie Risse blockieren, die Struktur verstärken und die Bildung und Ausbreitung von inneren Defekten verringern. Die Verstärkungswirkung hängt von verschiedenen Faktoren ab, darunter Fasertyp, Aspektverhältnis, Aufschlussverfahren, Verteilung, Ausrichtung und Bindungsstärke zwischen den Fasern und der Plattenmatrix.
Eine gleichmäßige Faserverteilung bildet ein zusammenhängendes Netzwerk innerhalb der Platte und maximiert die Verstärkung. Im Gegensatz dazu führt eine ungleichmäßige Verteilung zu zwei Problemen: Die Fasern verklumpen, was zu Unregelmäßigkeiten in der Dichte führt, die Wasseraufnahme erhöht und die Lebensdauer der Platte verkürzt, und die faserarmen Bereiche sind anfälliger für Schäden durch äußere Kräfte, was die Integrität der Platte beeinträchtigt.
Die Faserausrichtung beeinflusst die Festigkeit des Kartons. Wenn die Fasern während des Formens in einer bestimmten Richtung angeordnet werden, kann die Platte eine große Festigkeitsdifferenz zwischen Längs- und Querrichtung aufweisen, was die Gesamtqualität beeinträchtigt.
Die Bindungsstärke zwischen der Faser und der Matrix ist entscheidend für die Haltbarkeit. Studien zeigen, dass die Schnittstelle zwischen Fasern und Matrix der am meisten gefährdete Teil der Platte ist. Wenn die Fasern fest mit der Matrix verbunden sind, absorbieren sie mehr Aufprallenergie, was die Zähigkeit und Festigkeit der Platte deutlich erhöht. Zufällig orientierte Fasern verbessern die Kontinuität des Kartons und verringern interne Defekte, was die strukturelle Integrität des Kartons weiter stärkt.
Mit der Entwicklung von Kalziumsilikatplattenwurden die schädlichen Auswirkungen von Asbestfasern, die traditionell als Verstärkungsmaterial verwendet wurden, deutlich. Als Reaktion darauf begannen viele Länder 1969, die Verwendung von Asbest zu regulieren. Um diese Herausforderungen zu bewältigen, haben Forscher zunehmend alternative Verstärkungsfasern erforscht, z. B. Pflanzenfasern und Glasfasern, die heute allgemein anerkannt sind und die folgenden Eigenschaften aufweisen:
Gute Dispersion in Wasser: Die Fasern sollten sich gut in Wasser dispergieren lassen, wobei sich auf ihrer Oberfläche ein stabiler Wasserfilm bildet.
Alkalische Korrosionsbeständigkeit: Die Fasern müssen alkalischen Lösungen mit einem pH-Wert von 12-14 standhalten, da das Verfahren zur Herstellung von Kalziumsilikat stark alkalisch ist, was die Fasern stark angreifen kann.
Hohe Temperatur- und Druckbeständigkeit: Unter hydrothermalen Bedingungen sollten die Fasern die Kompatibilität mit der Matrix beibehalten und dabei eine ausreichende Festigkeit und Zähigkeit aufweisen.
Abb.7 Pflanzenfasern und Glasfasern
Die Fasern spielen zwar eine verstärkende Rolle, aber es gibt einen inhärenten Kompromiss zwischen Fasergehalt und Produktgewicht. Ein höherer Fasergehalt erhöht zwar die mechanische Festigkeit, erhöht aber auch das Gewicht des Produkts, wodurch sich seine Wärmedämmeigenschaften verringern. Umgekehrt bleibt das Produkt bei einem geringen Fasergehalt ultraleicht, aber die mechanische Festigkeit wird beeinträchtigt, so dass die Leistungsstandards möglicherweise nicht erfüllt werden. Außerdem wirkt sich die Faserdotierung auf die Produktionskosten aus. Daher ist die Bestimmung des optimalen Fasergehalts von entscheidender Bedeutung, um die mechanische Festigkeit und die ultraleichten Eigenschaften von harten Kalziumsilikaten auszugleichen.
Das Verständnis der Zusammensetzung von Kalziumsilikatplatten gibt Aufschluss über ihre Haltbarkeit, Wärmebeständigkeit und Anpassungsfähigkeit an verschiedene Anwendungen. Von der Faserverstärkung bis zur sorgfältigen Kontrolle des Materialverhältnisses spielt jede Komponente eine entscheidende Rolle bei der Erreichung der gewünschten Leistung. Wenn Sie weitere Fragen haben oder zusätzliche Informationen über Kalziumsilikatplatten benötigen, wenden Sie sich bitte an unsere Experten unter FireSafe.