Después de haber trabajado en más de 100 proyectos de protección contra incendios, entre los que se incluyen torres de oficinas, instalaciones industriales y centros de transporte, hemos aprendido que acertar con el corte es fundamental. placas de silicato cálcico no se trata sólo de herramientas y ángulos. Se trata de saber qué funciona en las condiciones reales del lugar de trabajo.
Esta guía no es teoría. Es el saber destilado que hemos acumulado en obras desordenadas, donde los bordes limpios, los ajustes ajustados y la presión del tiempo son la norma.
Por qué el recorte merece más atención
Hemos visto demasiadas instalaciones que se han ido al traste porque los cortes se hicieron con prisas o con la cuchilla equivocada. El corte afecta a mucho más que el aspecto de una tabla.
- El tiempo ahorrado más tarde empieza aquí: Un corte limpio ahora ahorra 20 minutos de ajustar, lijar o desechar una tabla más tarde.
- El ajuste afecta a la función: Una mala alineación implica espacios de aire, ajustes flojos y conexiones débiles que podrían comprometer el rendimiento de la ignifugación.
- Los bordes limpios contribuyen a la resistencia al fuego: Los bordes astillados o agrietados pueden actuar como vías de calor. En la mayoría de los trabajos, sellamos las líneas de corte con sellador cortafuegos para mantener el rendimiento.
Qué herramientas de corte funcionan realmente en el campo
Hemos utilizado de todo, desde sierras manuales en andamios hasta líneas CNC completas en talleres prefabricados. Esto es lo que siempre ha funcionado:
Seccionadoras CNC
Cuando producimos lotes o necesitamos tolerancias muy ajustadas, las máquinas CNC son la solución.
- Precisión guiada por ordenador: ±0,5 mm
- Maneja perfiles complicados como biseles o recortes
- La programación es rápida una vez que tienes tu CAD listo
- Funciona bien en fábrica, pero no tanto en el lugar de trabajo
Sierras de mesa deslizantes
Fiable para cortes rectos in situ o en pequeños talleres.
- Ideal para volúmenes medios y cortes rectangulares
- Buena repetibilidad
- Mayor facilidad para formar a los operarios
Sierras circulares manuales
Si tiene que cortar en un andamio, en un rincón estrecho o realizar trabajos de adaptación, esto es lo que utilizamos.
- Súper móvil y adaptable
- Utilice siempre un aspirador y un EPI
- Solemos llevar cuchillas de repuesto por si acaso.
Nota sobre el mundo real: En proyectos internacionales, a menudo utilizamos sierras circulares portátiles y aspiradoras HEPA. Una configuración sencilla, pero un trabajo limpio.
La selección de la hoja depende de la densidad de la placa
La densidad del tablero determina qué cuchilla no lo hará pedazos. Esto es lo que nos ha funcionado:
Densidad | Tipo de cuchilla | Detalles |
---|---|---|
300-500 kg/m³
|
Metal duro de dientes planos o alternos
|
Menos rebabas, mejor evacuación de virutas
|
500-800 kg/m³
|
Compuesto de punta plana o diamante (PCD)
|
Evita el agrietamiento de los bordes, sirve para ángulos
|
800-1000 kg/m³
|
Sólo diamante, diente ultrafino
|
Necesario para tableros más duros y densos
|
- Paso: 3-6 mm
- Tamaño de la hoja: 350 mm estándar
- Grosor del PCD: al menos 3,2 mm para una larga vida útil
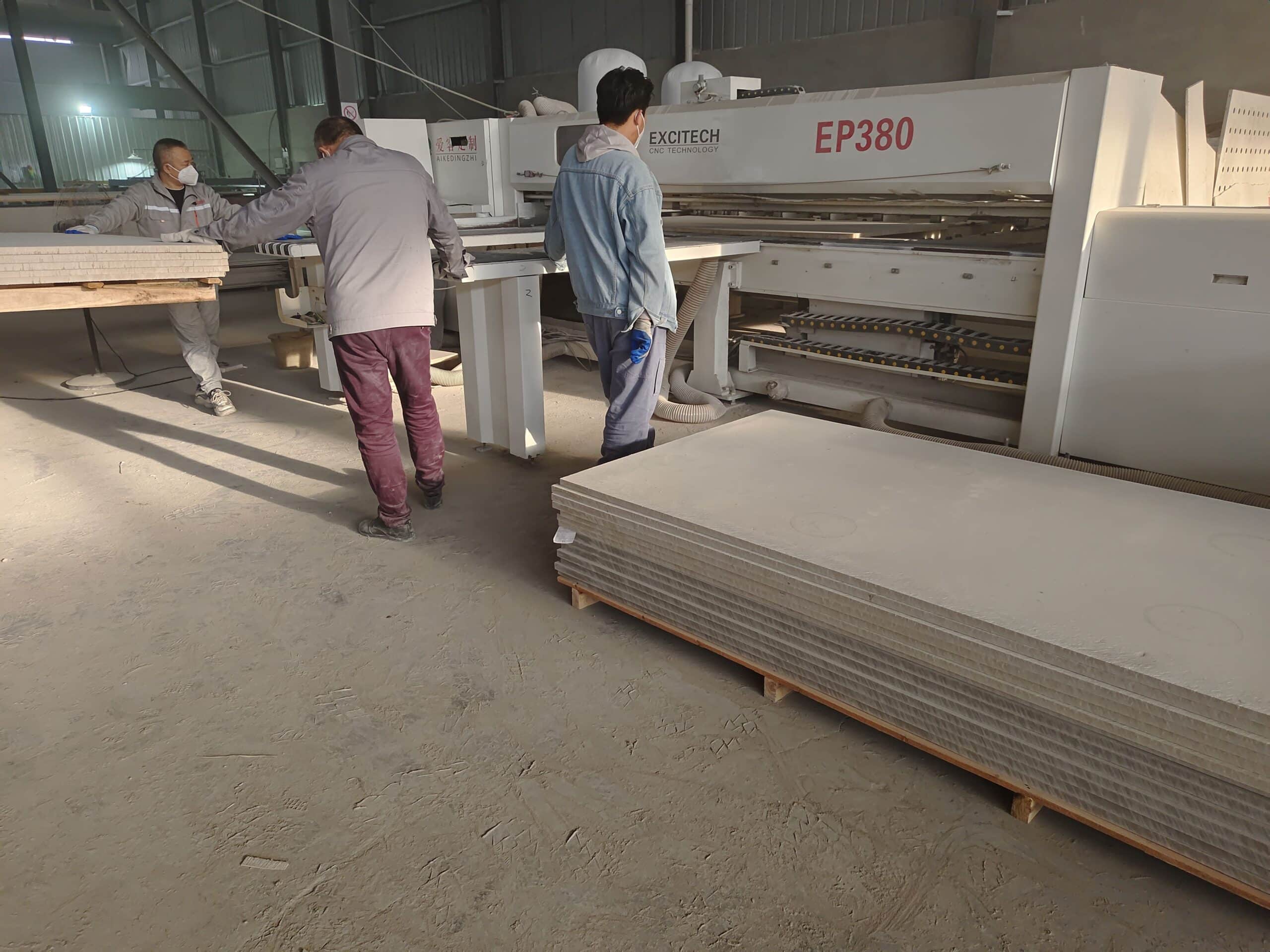
Nuestro proceso paso a paso (que realmente funciona)
Marcar la línea
Vuelve a comprobar las dimensiones y traza la línea con una escuadra y una cinta métrica. Para las partes irregulares, trazamos a partir de una plantilla de cartón.
Suavizar el borde
Utilice papel de lija de grano 120 o una recortadora. Solemos dar a los bordes biselados un ángulo de 15°: limpio y funcional.
Pasar el corte
Coloque la tabla boca abajo. Alimente la cuchilla constantemente a lo largo de la línea marcada; no se detenga a mitad de camino a menos que desee que se astille el borde.
Velocidad de avance: 10-20 m/min es el punto óptimo en la mayoría de los casos.
Uso del CNC para formas especiales o trabajos de volumen
Para núcleos de puertas cortafuegos, respaldos de armarios o paneles perforados, el fresado CNC es insuperable.
- Precisión: ±0,15 mm para la forma, ±0,1 mm para la colocación de los orificios
- Ahorro de tiempo: Los cambiadores automáticos de herramientas (ATC) ayudan con los cortes de varios pasos.
- Consistencia: La detección láser de bordes mantiene el astillado bajo control
- Cambios rápidos: Cambiamos las especificaciones entre lotes sin demora
Lo utilizamos sobre todo para componentes que deben tener un aspecto limpio y ajustarse a tolerancias estrictas.
Lo que siempre vigilamos in situ
Seguridad personal
- Llevar siempre una mascarilla N95, gafas y protección auditiva.
- Cortar en espacios bien ventilados
- Utilizar un extractor de polvo móvil siempre que sea posible
Seguridad contra incendios
- Sin materiales inflamables a menos de 5 metros
- Mantenemos una manta de fuego debajo de la estación de la sierra como una regla
Mantenimiento de las cuchillas
- Si oye quejidos o ve marcas de quemaduras, cámbielo inmediatamente.
- Sustituir o reafilar las cuchillas cada 400-500 metros de longitud de corte
Problemas comunes y lo que hacemos al respecto
Qué está fallando | Causa probable | Qué hacemos |
---|---|---|
Bordes deshilachados o astillados
|
Cuchilla embotada / avance incorrecto
|
Afilar o cambiar la cuchilla, cortar más despacio
|
Cortes no rectos
|
El tablero se desplazó durante el corte
|
Utilizar abrazaderas, mesa de succión o cinta adhesiva
|
Bordes quemados
|
Cuchilla demasiado caliente
|
Añadir refrigerante o reducir la velocidad
|
Polvo por todas partes
|
Extractor débil
|
Utilice un sistema de 2000m³/h como mínimo
|
Grietas en las esquinas
|
Radio de esquina estrecho
|
Pretaladre y utilice cortes escalonados; mantenga el radio interior ≥5 mm.
|
Palabras finales desde el lugar de trabajo
Corte placas de silicato cálcico no es cuestión de perfección, sino de constancia, seguridad y adaptabilidad. Con la configuración y los hábitos adecuados, obtendrá cortes limpios y menos problemas de instalación en el futuro.
Si está trabajando en un proyecto y necesita ayuda para elegir herramientas, configurar una rutina CNC o resolver un problema de corte específico, no dude en ponerse en contacto con nosotros. Estaremos encantados de compartir sus experiencias sobre el terreno y ayudarle a hacerlo bien a la primera.