Los tableros de silicato cálcico reforzados con fibras se fabrican a partir de fibras minerales inorgánicas o de celulosa combinadas con calcio y sílice como principales materiales cementantes. Estos materiales se someten a un proceso de despulpado, moldeado y posterior curado a alta temperatura y presión en vapor saturado, lo que forma coloides de silicato cálcico que se solidifican en tableros duraderos.
Entonces, ¿cómo se forma exactamente el silicato cálcico y qué papel desempeñan las fibras de refuerzo en el tablero? Basándome en mi experiencia, a continuación explicaré detalladamente cada aspecto.
Mecanismo de formación del silicato cálcico
El silicato cálcico se sintetiza mediante una reacción hidrotérmica entre materiales de calcio y sílice. La fuente de calcio, normalmente cal (CaO), incluye materiales como la cal, la cal apagada y la escoria de carburo de calcio. La fuente de sílice, compuesta principalmente de SiO₂, incluye tierra de diatomeas, polvo de cuarzo y cenizas volantes.
En la práctica, la producción de placas de silicato cálcico suele incorporar una pequeña cantidad de cemento para mejorar la moldeabilidad y el control. En la actualidad, la mayoría de los fabricantes utilizan una mezcla de cal y cemento, sustituyendo parte de la cal por cemento para mejorar el control de la producción. La reacción hidrotérmica del silicato cálcico en este sistema de cal-cemento se ilustra en la Fig. 1.
El mecanismo de reacción del silicato cálcico, como se muestra en la figura 2, puede dividirse en tres etapas principales:
Fase de precurado a presión normal: En esta fase inicial, el cemento reacciona en agua para formar silicato dicálcico (C₂S) y silicato tricálcico (C₃S). En condiciones ambientales, el C₂S se hidrata para producir C₂SH₂, mientras que el C₃S se hidrata para formar silicato cálcico hidratado altamente alcalino (C₂SH₂) y Ca(OH)₂, aunque estos compuestos no suelen reaccionar significativamente con el material de sílice.
Etapa de curado en autoclave: Al aumentar la temperatura y la presión, el material de sílice comienza a disolverse rápidamente y reacciona con Ca(OH)₂ para formar silicato cálcico hidratado altamente alcalino (C₂SH(A)), consumiendo Ca(OH)₂ en el proceso. A temperaturas elevadas, el C₂SH(A) es inestable y reacciona con el SiO₂ restante para convertirse en silicato cálcico hidratado de baja alcalinidad (C₂SH(B)), formando nuevos cristales que crecen continuamente hasta convertirse en cristales estables de tobermorita (C₅S₆H₅).
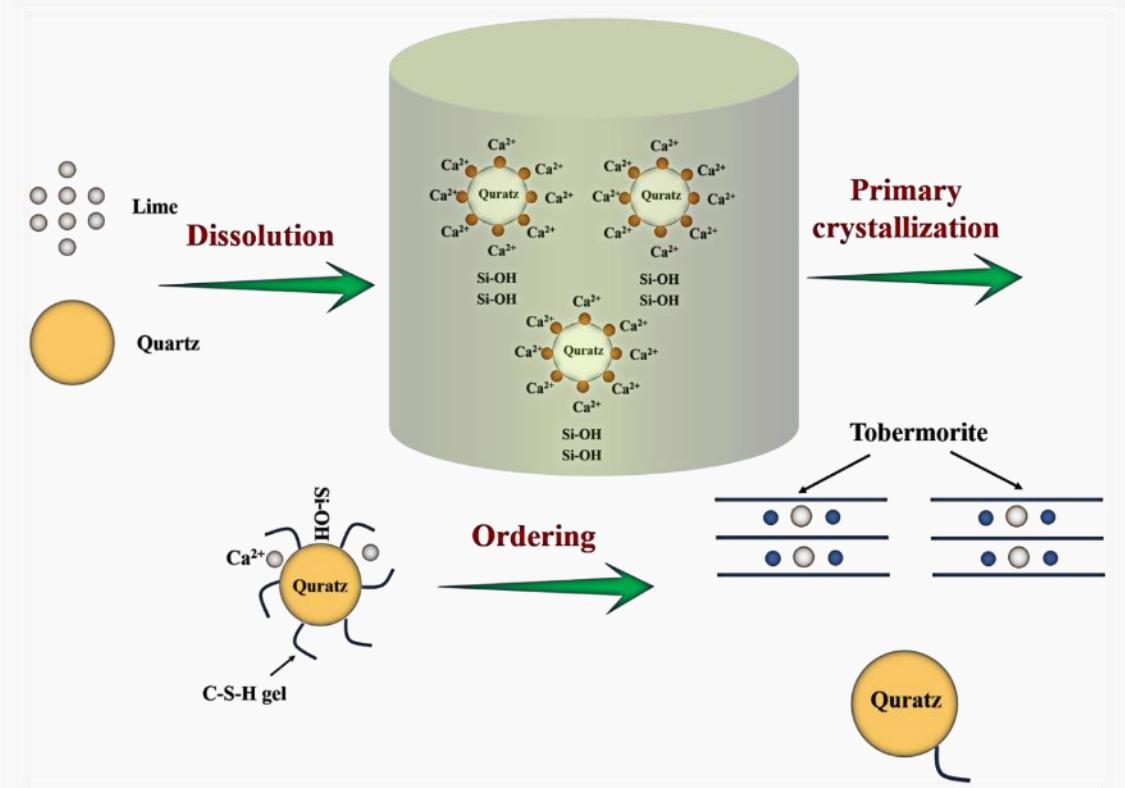
Fase de curado ampliada: Con un curado prolongado en autoclave, los cristales de tobermorita reaccionan además con SiO₂ para producir xonotlita (C₆S₆H), un silicato cálcico duro. Cabe destacar que, debido a la adición de cemento, el sistema de reacción se vuelve más complejo. En la síntesis hidrotermal real, compuestos como el aluminato cálcico y el yeso del agua, así como la alúmina de la arena de cuarzo, pueden dar lugar a un sistema de reacción cuaternario (CaO-SiO₂-Al₂O₃-H₂O) o incluso quinario (CaO-SiO₂-Al₂O₃-CaSO₄-H₂O). En consecuencia, los productos hidrotermales finales no son una simple mezcla de tobermorita y ettringita, sino que también pueden incluir silicato sódico y otros hidratos de silicato cálcico que contienen aluminio. Sin embargo, debido a la estabilidad y a la excelente estructura cristalina de la tobermorita, sigue siendo el principal hidrato en los tableros de silicato cálcico, permitiéndose algo de C₂SH(B) para garantizar unas propiedades físicas y mecánicas óptimas.
Diferencias entre tobermorita y xonotlita
La tobermorita y la xonotlita son dos tipos principales de silicatos cálcicos hidratados con propiedades distintas. La xonotlita presenta una contracción mínima y la mayor resistencia a la flexión entre los materiales de silicato cálcico, aunque requiere temperaturas de síntesis más altas y tiempos de procesamiento más largos en comparación con la tobermorita y el CSH(B).
Los productos de tobermorita, sintetizados normalmente mediante métodos hidrotérmicos estáticos, tienen una resistencia térmica limitada (hasta 650°C) y una densidad relativamente alta, lo que los hace adecuados principalmente para la industria petroquímica.
Los productos de xonotlita, en cambio, se sintetizan mediante métodos hidrotérmicos dinámicos, lo que les confiere una excelente resistencia a las altas temperaturas (hasta 1000 °C) y una baja densidad. Además, las fibras de xonotlita son biosolubles, lo que garantiza un alto nivel de seguridad. Con estas ventajas, la xonotlita se utiliza ampliamente en industrias de alta temperatura, como la metalurgia, la ingeniería química y los materiales de construcción. La serie de placas ignífugas de FireSafe es un ejemplo de placas de silicato cálcico a base de xonotlita de alta calidad.
El silicato cálcico duro se forma como cristales prismáticos o como agregados fibrosos alineados paralelamente al eje b. Al microscopio químico o electrónico, los cristales sintéticos de silicato cálcico duro aparecen como escamas. Los cristales fibrosos tienen radios de varios cientos de nanómetros y longitudes que alcanzan varios miles de nanómetros. A pesar de su estructura fibrosa, estos cristales no forman vacíos con radios de decenas de micras, sino que se aglomeran en estructuras esféricas huecas. Muchos de estos aglomerados alcanzan diámetros de decenas de micrómetros, formando huecos con radios de 10-30 μm. Los aglomerados esféricos de mayor tamaño crean huecos internos más sustanciales y espacios más amplios entre los agregados, lo que se traduce en una menor densidad aparente a medida que aumenta el diámetro del aglomerado.
La estructura de aglomerado esférico desempeña un papel crucial en la consecución de la densidad ultrabaja del material. Este material suele formarse prensando y secando una pasta de silicato cálcico duro. Durante el proceso de filtrado y prensado, los finos cristales fibrosos de silicato cálcico se dispersan por el flujo de agua, lo que reduce los espacios entre los cristales y aumenta la densidad debido a las fuerzas capilares.
Sin embargo, cuando estos cristales fibrosos forman aglomerados esféricos, el flujo de agua durante el filtrado-prensado no puede alinearlos direccionalmente. Esto proporciona a los aglomerados la fuerza suficiente para resistir una compresión excesiva. Durante el secado, los grandes espacios entre las esferas aceleran la evaporación del agua e impiden la compactación sin restricciones de las fibras, lo que reduce las fuerzas capilares excesivas. Esto minimiza la contracción y garantiza que el material siga siendo ultraligero.
Mecanismo y requisitos de rendimiento del refuerzo de fibra
Los materiales de fibra mejoran los tableros de silicato cálcico bloqueando las grietas, endureciendo la estructura y reduciendo la formación y propagación de defectos internos. El efecto de refuerzo depende de varios factores, como el tipo de fibra, la relación de aspecto, el tratamiento de la pasta, la distribución, la orientación y la fuerza de unión entre las fibras y la matriz del tablero.
Una distribución uniforme de las fibras forma una red interconectada dentro del tablero, maximizando el refuerzo. Por el contrario, una distribución desigual provoca dos problemas: la aglomeración de fibras, que causa inconsistencias de densidad, aumenta la absorción de agua y acorta la vida útil del tablero; y las zonas con deficiencias de fibras, que son más susceptibles de sufrir daños por fuerzas externas, lo que compromete la integridad del tablero.
La orientación de las fibras afecta a la resistencia del cartón. Si las fibras se disponen direccionalmente durante el moldeo, el cartón puede presentar una gran disparidad de resistencia entre las direcciones longitudinal y transversal, lo que reduce la calidad general.
La fuerza de unión entre la fibra y la matriz es crucial para la durabilidad. Los estudios demuestran que la interfaz fibra-matriz es la parte más vulnerable de la tabla. Cuando las fibras se unen fuertemente a la matriz, absorben más energía de impacto, lo que aumenta significativamente la dureza y resistencia de la tabla. Las fibras orientadas aleatoriamente mejoran la continuidad del tablero y reducen los defectos internos, reforzando aún más su integridad estructural.
Con el desarrollo de placas de silicato cálcico...se hicieron evidentes los efectos nocivos de las fibras de amianto, utilizadas tradicionalmente como material de refuerzo. En respuesta, muchos países empezaron a regular el uso del amianto en 1969. Para hacer frente a estos problemas, los investigadores han explorado cada vez más fibras de refuerzo alternativas, como las fibras vegetales y las fibras de vidrio, que ahora se reconocen ampliamente por reunir las siguientes propiedades:
Buena dispersión en agua: Las fibras deben dispersarse bien en el agua, formándose una película acuosa estable en su superficie.
Resistencia a la corrosión alcalina: Las fibras deben soportar soluciones alcalinas con un pH de 12-14, ya que el proceso de preparación del silicato cálcico es altamente alcalino, lo que puede corroer gravemente las fibras.
Resistencia a altas temperaturas y presiones: En condiciones hidrotérmicas, las fibras deben mantener la compatibilidad con la matriz, junto con una resistencia y tenacidad suficientes.
Fig.7 Fibra vegetal y fibra de vidrio
Aunque las fibras desempeñan una función de refuerzo, existe un equilibrio inherente entre el contenido de fibra y el peso del producto. Un mayor contenido de fibra aumenta la resistencia mecánica, pero también incrementa el peso del producto, reduciendo sus propiedades de aislamiento térmico. A la inversa, un bajo contenido de fibra mantiene el producto ultraligero pero compromete su resistencia mecánica, lo que puede hacer que no cumpla las normas de rendimiento. Además, el dopaje de las fibras repercute en los costes de producción. Por tanto, determinar el contenido óptimo de fibra es crucial para equilibrar la resistencia mecánica y las propiedades ultraligeras de los materiales de silicato cálcico duro.
Entender la composición de las placas de silicato cálcico permite comprender su durabilidad, resistencia térmica y adaptabilidad a diversas aplicaciones. Desde el refuerzo de fibra hasta el control cuidadoso de las proporciones de los materiales, cada componente desempeña un papel crucial en la consecución del rendimiento deseado. Si tiene alguna pregunta o necesita más información sobre las placas de silicato cálcico, no dude en ponerse en contacto con los expertos de FireSafe.