Panneau de silicate de calcium est composé de fibres minérales inorganiques ou de fibres de cellulose, associées à d'autres fibres courtes en vrac comme matériaux de renforcement. La silice et les composés de calcium sont les principaux agents liants. Le processus de production comprend le dépulpage, le moulage et une réaction de durcissement accéléré sous vapeur saturée à haute température et à haute pression, ce qui permet d'obtenir une feuille de silicate de calcium durable.
En ajustant les ratios de matières premières et les processus de production, panneaux de silicate de calcium avec des caractéristiques variées peuvent être produites pour répondre à diverses exigences d'application. Cette adaptabilité garantit que le matériau convient à différentes conditions de travail. Comment un panneau de silicate de calcium est-il préparé exactement et comment les méthodes de production influencent-elles ses performances ?
Processus de production de panneaux de silicate de calcium
Après des décennies de développement, le processus de production des panneaux de silicate de calcium a été normalisé et rationalisé. Les principales étapes comprennent la préparation des matières premières, le dépulpage, le moulage des feuilles, le durcissement en autoclave et le post-traitement. Voici un aperçu du processus :
Préparation des matières premières
Cette étape comprend
Broyage de sable de quartz par voie humide: Pour obtenir la finesse requise pour la mise en pâte.
Ébullition de la chaux vive: Assure une réactivité optimale.
Traitement des matériaux fibreux: Broyer et disperser les fibres pour améliorer l'uniformité.
Mise en pâte
La pâte de fibres est mélangée à des matériaux à base de calcium et de silice dans un mélangeur à contre-courant afin d'obtenir une dispersion uniforme. Le mélange est converti en une boue à concentration constante, qui est stockée dans un réservoir de pâte. Certains fabricants traitent ensuite la suspension à l'aide de broyeurs afin de garantir un mélange homogène des fibres et des particules.
Moulage en feuille
La boue est distribuée sur un tapis roulant et déshydratée pour former de fines couches de découpes. Ces couches sont enroulées autour d'un cylindre de moulage jusqu'à l'épaisseur souhaitée. Une fois que la dalle a atteint les dimensions spécifiées, un système de coupe automatisé la découpe, puis les dalles sont empilées et pressées pour renforcer leur résistance et leur compacité.
Polymérisation en autoclave
Les dalles sont placées dans un autoclave, où elles subissent une réaction chimique impliquant de la silice, de l'hydroxyde de calcium et de l'eau. Cette réaction forme des cristaux de Tobermorite et du silicate de calcium dur, qui sont essentiels pour la solidité, la stabilité dimensionnelle et la résistance à l'humidité du panneau.
Séchage et post-traitement
Après le durcissement, les plaques sont séchées pour atteindre le taux d'humidité standard. Les contrôles de qualité finaux garantissent que seuls les produits conformes sont livrés sous forme de plaques de silicate de calcium finies.
Dans ce processus, moulage en feuille et durcissement en autoclave sont particulièrement critiques pour la qualité du produit final. Ces étapes influencent directement la solidité, le taux de dilatation et la résistance à l'humidité du panneau, ce qui en fait le point central de l'optimisation du processus.
Les sections suivantes se concentrent sur ces deux processusLes résultats de l'étude ont été présentés à la Commission européenne, en soulignant leur influence sur les performances des panneaux en silicate de calcium.
Processus de découpage et de moulage
Après l'étape de dépulpage, la boue mélangée est distribuée, déshydratée et moulée par extrusion pour former des panneaux de silicate de calcium. Le processus de découpage est principalement divisé en deux méthodes, la première étant le moulage par extrusion et la seconde, le moulage par extrusion. Méthode de copie étant l'un des plus utilisés.
Méthode de copie
La méthode de copiage, un type de procédé humide, a été introduite pour la première fois par Hatschek au début du 20e siècle pour la production de matériaux composites en fibre-ciment. Au fil des ans, ce procédé a été affiné et reste une approche clé dans la production de panneaux de silicate de calcium.
La ligne de production de la méthode de copie comprend trois sections principales :
Section de mise en pâte: Préparation de la boue.
Section de la boîte à mailles: Forme les couches vierges.
Section de traitement en blanc: Transforme les ébauches en produits finis.
Comme indiqué dans Fig. 4Le processus de copie commence par la mécanisme de la roue à filetqui transfère la pâte préparée sur une couverture industrielle. La couverture transporte la pâte vers les sections de déshydratation et de moulage par extrusion. Le cylindre de la machine de moulage comprime et compacte les ébauches. Lorsque la couverture industrielle se détache du cylindre de moulage, une pression négative est créée entre l'ébauche et la surface du cylindre, ce qui permet à l'ébauche d'adhérer étroitement au cylindre de moulage. Lorsque l'épaisseur souhaitée est atteinte, l'ébauche est découpée et passe à l'étape suivante de la production.
Avantages et limites
Le processus de copiage produit des panneaux de silicate de calcium avec :
Distribution uniforme des couches: Assurer une qualité constante des matériaux.
Haute résistance et planéité: Assure une excellente intégrité structurelle et une surface lisse.
Toutefois, cette méthode nécessite une grande surface de production, consomme beaucoup d'énergie et implique une maintenance complexe.
Méthode de la pâte à papier en flux
La méthode du flow pulp, tout comme la méthode de copiage, fait partie de la catégorie des procédés humides. Si le processus de production global est largement similaire à celui de la méthode de copiage, la principale différence réside dans la manière dont la pâte est distribuée. Au lieu d'utiliser une roue à filet pour le transfert de la pâte, la méthode du flow pulp s'appuie sur une boîte de flow pulp comme mécanisme de base.
Dans ce processus, la boue pré-mélangée est pompée dans la boîte de pâte à écoulement, qui l'étale uniformément sur une couverture industrielle. La couverture transporte ensuite la boue à travers plusieurs boîtes de déshydratation sous vide avant de l'acheminer vers la machine à mouler les panneaux de silicate de calcium pour l'extrusion, la déshydratation et le moulage.
L'un des avantages de la boîte à pulpe à écoulement est sa capacité à maintenir un débit constant sur toute la largeur du blanchet, ce qui empêche l'écoulement latéral et assure une distribution uniforme de la boue. Il en résulte une vitesse d'encollage constante sur toute la largeur du blanchet, sans aucune fluctuation.
Le diagramme de processus pour la méthode de la pâte à papier est illustré dans le tableau suivant Figure 6.
Lorsque la boue s'écoule de la boîte à pulpe sur le blanchet industriel, sa teneur élevée en humidité nécessite un nombre accru de ventouses de déshydratation sous vide dans la ligne de production. Cela peut entraîner une légère réduction de la planéité et de la résistance du produit. Toutefois, par rapport à la méthode de copiage, la méthode de la pâte fluide nécessite moins d'espace et consomme relativement moins d'énergie.
Comparaison avec la méthode de copie
Il est important de noter que les méthodes d'écoulement de la pâte et de copiage ne sont pas interchangeables. Le choix du procédé dépend des exigences de performance du produit final et de ses scénarios d'application. Une comparaison détaillée est présentée ci-dessous :
Aspect | Méthode de la pâte à papier en flux | Méthode de copie |
---|---|---|
Type de processus
|
Procédé humide
|
Procédé humide
|
Épaisseur de la couche
|
Des couches individuelles plus épaisses, moins de couches au total
|
Couches individuelles plus fines, couches totales plus nombreuses
|
Disposition des fibres
|
Les fibres perpendiculaires forment une structure de renforcement en 3D
|
Fibres alignées dans le sens de la bande
|
Résistance à la flexion
|
Légèrement inférieur
|
Plus élevé
|
Résistance à la compression/traction
|
Légèrement plus élevé
|
Plus bas
|
Consommation d'énergie
|
Plus bas
|
Plus élevé
|
Besoin d'espace
|
Plus petit
|
Plus grand
|
Planéité du panneau fini
|
Légèrement réduit
|
Haut
|
Facteurs clés influençant la qualité du conseil d'administration
Quelle que soit la méthode de production, le processus d'autoclavage joue un rôle essentiel. Au cours de cette étape, les composants siliceux et calciques de la dalle se transforment en cristaux de tobermorite chimiquement stables et en silicate de calcium dur. La teneur en cristaux détermine directement la qualité du panneau fini.
Facteur | Impact sur la qualité |
---|---|
Proportion de matières premières
|
Influence la formation de la tobermorite et des cristaux de silicate de calcium dur.
|
Processus de production des billettes
|
Affecte l'intégrité structurelle et l'uniformité des flans.
|
Processus d'autoclavage
|
Détermine la stabilité, le taux de dilatation et la résistance à l'humidité des panneaux.
|
En affinant ces variables, les fabricants peuvent produire panneaux de silicate de calcium Les systèmes de gestion de l'information sont conçus pour répondre aux besoins d'applications spécifiques, garantissant ainsi un équilibre optimal entre performance et efficacité.
Processus de compression de la vapeur
Méthode de synthèse hydrothermale
Dans la production de panneaux de silicate de calcium, les cristaux de silicate de calcium sont synthétisés par un processus hydrothermal dans un autoclave à haute température et à haute pression. Ce processus, connu sous le nom d'"entretien de l'autoclave", consiste à faire réagir des matériaux à base de silicium et de calcium à 180-200°C et 1-1,5 MPa pour 13-20 heures pour générer des cristaux stables.
La méthode de synthèse hydrothermale utilise l'eau comme milieu de réaction dans un environnement chimique en phase liquide. En fonction de l'agitation appliquée, la méthode est divisée en deux types : statique et dynamique.
Méthode statique:
Dans cette approche, les matières premières sont mélangées, moulées en plaques humides et préconditionnées avant l'étape de l'autoclave. Le processus de préconditionnement implique généralement
Température: 50-70°C
Durée de l'accord: 4-5 heures
Une fois que la dalle a acquis une résistance suffisante, elle est démoulée et envoyée dans l'autoclave pour la réaction hydrothermale.
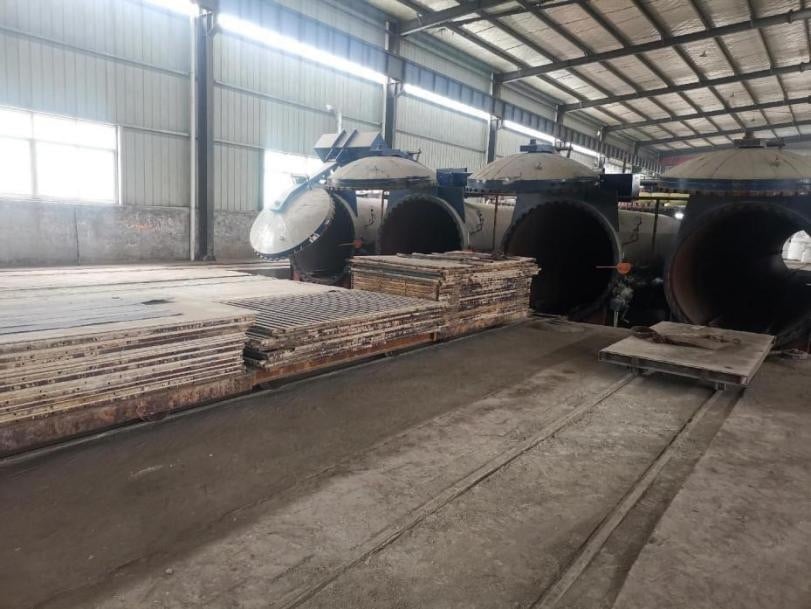
Méthode dynamique:
Cette méthode consiste à remuer les matières premières dans l'autoclave pendant la réaction. L'agitation continue maintient les particules solides en suspension dans la phase liquide, ce qui favorise la croissance et la dispersion uniformes des cristaux. Elle facilite également la formation de fibres de silicate de calcium dur de grand diamètre. Ces fibres ont tendance à s'entrelacer, créant ainsi des particules secondaires creuses qui contribuent à la formation du silicate de calcium :
Haute porosité: Améliore l'isolation thermique.
Faible conductivité thermique: Améliore l'efficacité énergétique.
Aspect | Méthode statique | Méthode dynamique |
---|---|---|
Processus
|
Réaction hydrothermale stationnaire après préconditionnement.
|
La réaction se produit sous agitation continue.
|
Croissance des cristaux
|
Produit des cristaux plus petits et moins uniformes.
|
Favorise la formation de cristaux plus gros et uniformément répartis.
|
Isolation thermique
|
Modéré
|
Élevée en raison de l'augmentation de la porosité et de l'enchevêtrement des fibres.
|
Coût de l'équipement
|
Investissement moindre.
|
Investissements plus élevés en raison de la complexité de l'équipement.
|
Le méthode dynamique offre des propriétés d'isolation thermique supérieures grâce à sa capacité à former des structures très poreuses, mais elle nécessite des équipements plus avancés et des coûts plus élevés. En revanche, le méthode statique est plus simple et plus rentable, ce qui le rend adapté aux projets ayant des exigences d'isolation standard.
Problèmes typiques et solutions dans le processus de vaporisation
De nombreux experts s'accordent à dire que, outre la formulation, la maîtrise du processus d'autoclavage est un facteur clé pour déterminer les performances des panneaux de silicate de calcium. Le processus de vaporisation implique la synthèse hydrothermique continue de matériaux siliceux et calcaires. Au cours de ce processus, de nouveaux cristaux se forment et les cristaux existants croissent, créant finalement des conidies cristallines avec une structure spatiale qui se lie étroitement aux fibres, assurant ainsi la solidité du panneau.
Toutefois, ce processus peut également introduire des défauts structurels qui réduisent la résistance du panneau et d'autres propriétés physiques. Ces défauts se manifestent principalement dans les domaines suivants :
1. Pression interne et relâchement structurel
Lorsque la planche se réchauffe pendant la vaporisation, l'eau et l'air contenus dans les pores internes se dilatent, ce qui génère une pression interne. À un certain stade, cette pression interne peut dépasser la pression externe de la vapeur.
En même temps, la croissance continue des cristaux conduit à grossissementoù se forment de plus grands cristaux. Cela réduit le nombre de points de liaison entre les cristaux, ce qui affaiblit la liaison cristalline et diminue la résistance. En outre, les contraintes de traction internes dues à la pression de cristallisation affaiblissent encore la structure. Ces effets combinés peuvent entraîner un relâchement de la structure et la formation de bulles et d'autres défauts dans le panneau.
2.Conseil Fissuration des bords
La fissuration des bords des panneaux est un défaut de fabrication important qui peut compromettre l'intégrité structurelle des panneaux de silicate de calcium. Les fissures apparaissent généralement le long des bords, pénétrant dans toute l'épaisseur du panneau et s'étendant de quelques centimètres à plusieurs pouces vers l'intérieur. Ce problème est principalement dû aux différences de température et d'humidité pendant la phase de décompression. Lorsque la température des bords descend en dessous de celle de l'intérieur, elle crée des contraintes destructrices qui entraînent l'apparition de fissures.
3. perte de résistance des fibres
La perte de résistance des fibres constitue un défi majeur dans la production de panneaux de silicate de calcium. Si le passage de l'amiante aux fibres végétales ou de verre répond aux préoccupations sanitaires, ces matériaux alternatifs posent des problèmes lors de l'autoclavage. Bien que le processus d'autoclavage soit essentiel pour créer des liaisons de silicate de calcium hydraté qui améliorent la résistance à la flexion, une exposition prolongée à des températures élevées et à des conditions alcalines peut dégrader l'intégrité de la fibre au fil du temps.
Optimisation des processus de fabrication
Pour relever efficacement ces défis, les fabricants doivent adopter une approche globale en trois phases :
Phase de pré-conditionnement
La mise en œuvre d'un processus d'arrêt statique ou de pré-conditionnement à la chaleur sèche est une étape préliminaire cruciale. Cela permet de réduire l'humidité interne, de minimiser les contraintes liées à la pression pendant l'autoclavage et d'améliorer la résistance structurelle du carton.
Gestion de la pression
Un contrôle précis de la réduction de la pression, en particulier pendant les dernières étapes de la pressurisation, est vital. Des changements de pression prématurés peuvent compromettre l'intégrité structurelle du carton avant qu'il n'atteigne sa résistance optimale.
Processus de séchage contrôlé
Un processus de flambage doux doit être utilisé pour atténuer les contraintes de température et d'humidité. Le processus doit être calibré pour favoriser la formation modérée de tobermorite dans l'hydrure, un traitement hydrothermique prolongé étant réservé aux panneaux nécessitant des propriétés améliorées.
L'approche de Firesafe
En tant que leader de l'industrie de la fabrication de panneaux de silicate de calcium, Sécurité incendie a mis au point des procédés exclusifs pour relever tous ces défis. Grâce à des techniques avancées de préservation des fibres et à des mesures rigoureuses de contrôle de la qualité, Firesafe fournit constamment des panneaux ignifuges en silicate de calcium qui dépassent les normes de l'industrie en matière d'intégrité structurelle et de performance.