Having worked on over 100 fire protection projects—including office towers, industrial facilities, and transport hubs—we’ve learned that getting the cut right on calcium silicate boards isn’t just about tools and angles. It’s about knowing what works under real job site conditions.
This guide isn’t theory. It’s the distilled know-how we’ve built up on messy construction sites, where clean edges, tight fits, and time pressure are the norm.
Why Cutting Deserves More Attention
We’ve seen too many installations go sideways because cuts were rushed or done with the wrong blade. Cutting affects far more than just how a board looks.
- Time saved later starts here: A clean cut now saves 20 minutes of adjusting, sanding, or tossing a board later.
- Fit affects function: Poor alignment means air gaps, loose fits, and weak connections that could compromise fireproofing performance.
- Clean edges help fire resistance: Chipped or cracked edges can act as heat paths. In most jobs, we seal cut lines with firestop sealant to lock in performance.
What Cutting Tools Actually Work in the Field
We’ve used everything from handheld saws on scaffolding to full CNC lines in prefab workshops. Here’s what has consistently delivered:
CNC Panel Saws
When we’re producing batches or need very tight tolerances, CNC machines are the go-to.
- Computer-guided precision: ±0.5mm
- Handles tricky profiles like bevels or cutouts
- Programming is fast once you have your CAD ready
- Works well in factory settings, less so on job sites
Sliding Table Saws
Reliable for straight cuts on-site or in smaller shops.
- Best for medium volumes and rectangular cuts
- Good repeatability
- Easier to train operators
Handheld Circular Saws
If you’re cutting on scaffolding, in a tight corner, or doing retrofit work—this is what we use.
- Super mobile and adaptable
- Always pair with a vacuum extractor and PPE
- We usually bring extra blades on site just in case
Real-world note: In international projects, we often spec portable circular saws + HEPA vacuums. Simple setup, but gets the job done cleanly.
Blade Selection Depends on Board Density
The board’s density dictates what blade won’t chip it to bits. Here’s what’s worked for us:
Density | Blade Type | Details |
---|---|---|
300–500 kg/m³
|
Flat-top or alternate tooth carbide
|
Fewer burrs, better chip clearance
|
500–800 kg/m³
|
Composite flat-top or diamond (PCD)
|
Prevents edge cracking, works for angles
|
800–1000 kg/m³
|
Diamond only, ultra-fine tooth
|
Needed for harder, denser boards
|
- Pitch: 3–6mm
- Blade size: 350mm standard
- PCD thickness: at least 3.2mm for long life
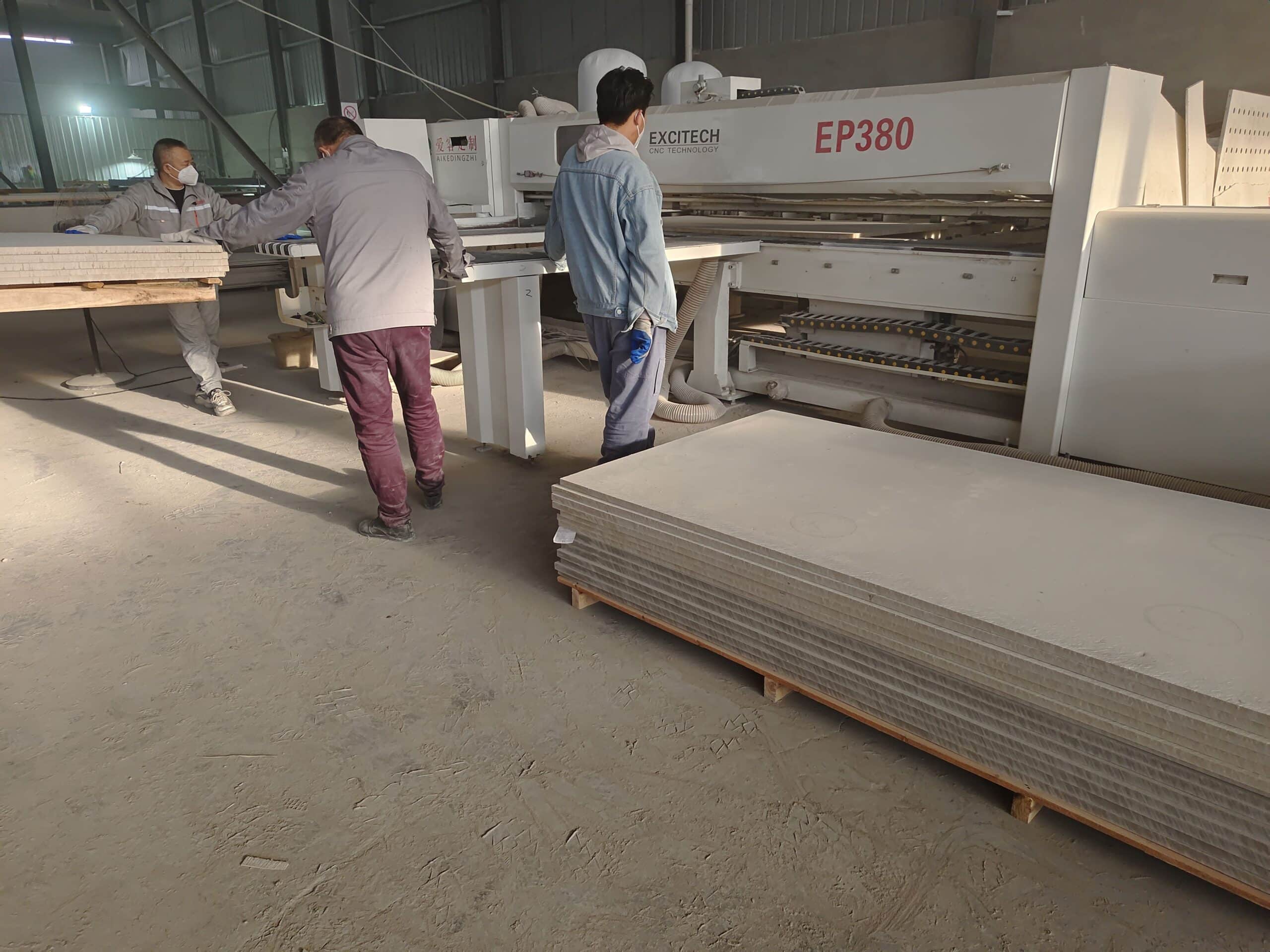
Our Step-by-Step Process (That Actually Works)
Marking the Line
Double-check your dimensions and draw the line with a square and tape measure. For irregular parts, we trace from a cardboard template.
Smoothing the Edge
Use 120-grit sandpaper or a trimmer. We usually give beveled edges a 15° angle—clean and functional.
Making the Cut
Lay the board face down. Feed the blade steadily along the marked line—don’t stop midway unless you want edge chipping.
Feed speed: 10–20m/min is the sweet spot in most cases.
Using CNC for Special Shapes or Volume Work
For fire door cores, cabinet backings, or perforated panels, CNC routing is unbeatable.
- Accuracy: ±0.15mm for shape, ±0.1mm for hole placement
- Time saver: Auto tool changers (ATC) help with multi-step cuts
- Consistency: Laser edge detection keeps chipping under control
- Fast switchovers: We change specs between batches without delay
We use this mostly for components that need to look clean and fit within tight tolerances.
What We Always Watch for on Site
Personal Safety
- Always wear an N95 mask, goggles, and hearing protection
- Cut in well-ventilated spaces
- Use a mobile dust extractor where possible
Fire Safety
- No flammable materials within 5 meters
- We keep a fire blanket under the saw station as a rule
Blade Maintenance
- If you hear whining or see scorch marks, swap immediately
- Replace or regrind blades every 400–500 meters of cut length
Common Problems and What We Do About Them
What’s Going Wrong | Likely Cause | What We Do |
---|---|---|
Frayed or chipped edges
|
Dull blade / wrong feed rate
|
Sharpen or replace blade, cut slower
|
Cuts not straight
|
Board shifted during cut
|
Use clamps, suction table, or tape
|
Burnt edges
|
Blade running too hot
|
Add coolant or reduce speed
|
Dust everywhere
|
Weak extractor
|
Use 2000m³/h system minimum
|
Cracks on corners
|
Tight corner radius
|
Pre-drill and use stepped cuts; keep inner radius ≥5mm
|
Final Word from the Job Site
Cutting calcium silicate boards isn’t about perfection—it’s about consistency, safety, and adaptability. With the right setup and habits, you’ll get clean cuts and fewer installation issues down the line.
If you’re working on a project and need help choosing tools, setting up a CNC routine, or solving a specific cut issue, feel free to reach out. We’re happy to share notes from the field—and help you get it right the first time.