Introduction
Have you ever worked with calcium silicate board? In my 12 years of experience, I’ve come to appreciate it as one of the most versatile materials for construction projects. Whether for walls or ceilings, it offers excellent fire resistance and moisture-proof properties. For instance, the FireSafe-500 is a product I’ve personally used on multiple projects. Its combination of cost-effectiveness, durability, and resistance to environmental factors makes it an ideal choice for both factory and residential buildings.
Materials for Installation
Before we dive into the calcium silicate board installation, let’s talk about the materials you’ll need. For wooden bases, you’ll need wood screws or nails.
If you’re working with a steel substrate, you’ll need self-tapping screws or machine screws. Obviously, you’ll additionally need the calcium silicate board itself.
In many cases, you might also need adhesives, such as FireSafe-1808, a modified, ceramic-based adhesive understood for its high-temperature bond. The use of adhesives relies on the specific process and design needs of your project.
For projects needing sound insulation and thermal insulation, materials like glass cotton and rock cotton are usually made use of. These materials can be included as an insulation layer to boost the efficiency of your fire proof system.
Calcium silicate boards offer excellent fire resistance, making them a cost-effective solution for a wide range of construction applications. Depending on the specific demands of your project, additional materials may be required to meet performance and safety standards. It is essential to evaluate the unique requirements of each project to ensure a secure and efficient installation, while adhering to all relevant building codes and regulations.
For more detailed information on the properties and uses of calcium silicate boards, you can check out my previous article: What is Calcium Silicate Board?.
Preparation Steps
Before you begin the install of the calcium silicate board, see to it your base material is ready. Whether it’s a wood base or a steel base, the board material can be fastened directly to it. The distance between the fasteners and the substrate will depend on the component used and the plate thickness, so make sure you have the dimensions required.
When screwing the corners, focus on the spacing and position of the fasteners. It’s important to make sure that the board is fixed at multipoint simultaneously to ensure stability. If you’re attaching something to the calcium silicate board, see to it it’s attached to the base material.
For ceiling construction, the substrate should be perpendicular to the fiber direction of the calcium silicate board. This is an essential detail to keep in mind when you install calcium silicate board on the ceiling.
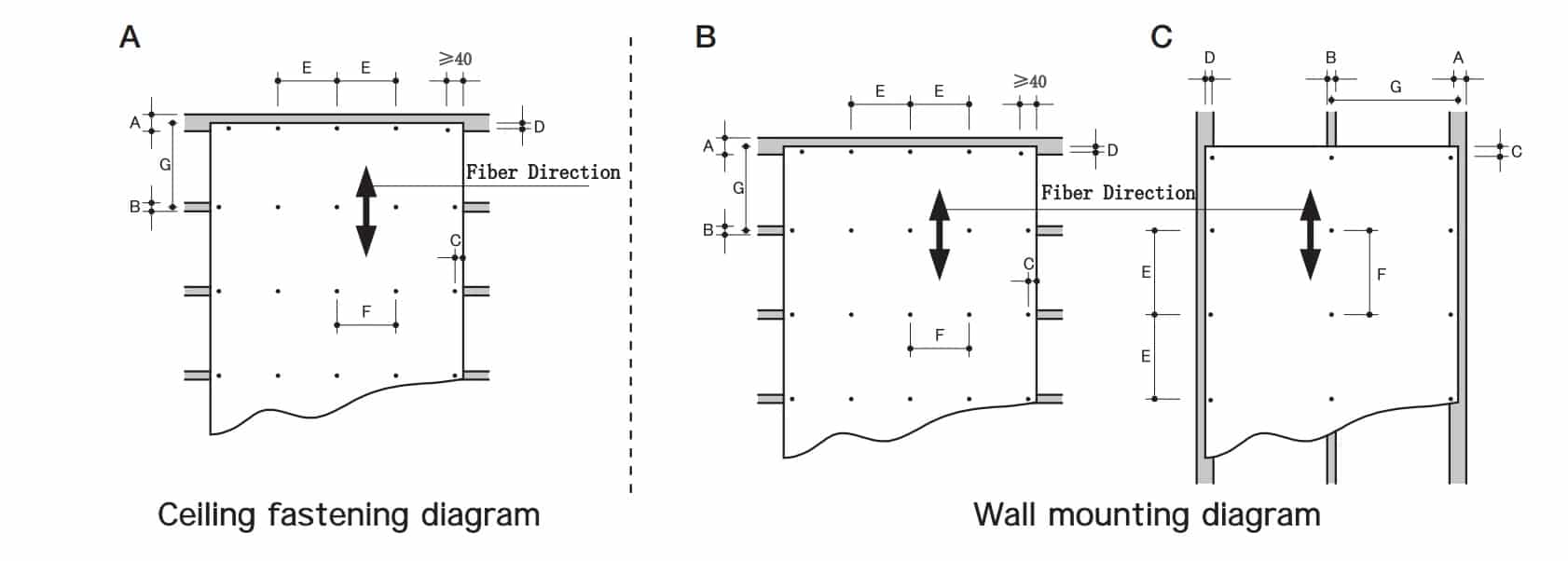
Handling of calcium silicate boards
1.Setting Up the Work Area
Prior to beginning the installation process, guarantee that your working environment is equipped with a dust collector. When cutting or shaping the FireSafe-500 calcium silicate boards, it can generate dust, which you need to manage effectively to avoid generating too much dust and maintain a clean and safe workspace.
2.Safety Measures
Safety should always be your priority when working with any type of building and construction material, including the FireSafe-500. Prior to starting, make sure you have the following personal protective equipment:
- Masks: To protect you from inhaling any dust particles.
- Face Shields and Goggles: To protect your face and eyes from any flying debris during cutting or drilling.
- Safety Shoes: To protect your feet from any falling objects.
- Work Clothes: To shield your body from dust and debris.
3.How to Cut Calcium Silicate Boards Safely and Efficiently
For cutting the board, I used a slate saw and an electric motor with a dust collector. When performing harsh cutting, I made a few cuts with a cutter on the front and rear of the board, then bent it. This procedure makes sure that the board face is not damaged.
4.Drilling Tips
For drilling small openings, I used a hand drill or an electrical drill. After using a hole saw or drilling a small opening, I cut out the rest with a jigsaw. Bear in mind, when drilling, it’s important to fix the board securely to prevent any movement.
5.Finishing
After cutting and drilling, I finished the sides with a file and sandpaper. This action is very important to smooth out any rough edges and guarantee a clean finish on all sides of the board.
Wall Construction
Before starting the partition wall construction, the substrate should be inspected for any looseness or unevenness. It’s also important to check the foundation reinforcement, especially around openings like windows and doorways, to ensure stability. Wall height should be considered to maintain structural integrity. Accurate marking based on the construction drawings helps minimize material waste during allocation. When dealing with openings such as doors, avoid cutting the calcium silicate board from one end to the other in a single piece.
For cutting the calcium silicate board, tools like a board cutter, jigsaw, dedicated saw, or a portable electric saw with a dust collector are recommended. The general mounting method and fastening intervals for calcium silicate boards are shown below. A crucial step when fastening the board to the substrate is to securely attach one side first to ensure overall stability.
Ceiling Construction
Similar to the wall construction process, the substrate was thoroughly inspected before beginning the ceiling installation. Accurate marking was done according to the construction drawings to ensure precision. The same tools—board cutter, jigsaw, dedicated saw, and portable electric saw with a dust collector—were used for cutting the calcium silicate board. The general mounting method and fastening intervals for the boards are outlined below. Installation began from the center of the ceiling, gradually working outward toward the edges to ensure even elevation across the surface.
Finishing
For the finishing stage, a sealer was applied after surface preparation before painting. For general interior applications, interior synthetic resin emulsion paint, acrylic resin paint, or urethane resin paint was used. In areas prone to moisture, such as kitchens and dressing rooms, exterior-grade synthetic resin emulsion paints, acrylic resin paints, or urethane resin paints were chosen. Oil-based paints, phthalate resin paints, and lacquer paints were avoided due to the alkaline nature of calcium silicate boards. Non-formaldehyde paints were selected for safety.
For a cloth finish, a sealer was similarly applied after surface preparation. An adhesive suitable for the finishing material (such as wallpaper or cloth) was used, ensuring it was non-formaldehyde.
For a tile finish, a sealer was applied following surface preparation. To minimize movement at the joints during seismic events, two base boards were used as a general rule. Tiles with a height of less than 5 meters were installed, and mechanical fall prevention measures were applied when necessary.
Conclusion
And that’s the process of installing calcium silicate board. While it may seem like several steps, with the right tools and a bit of patience, the task becomes much more manageable. This guide should provide helpful insights for your own installation project. For any questions or additional information about calcium silicate boards, feel free to reach out to the experts at FireSafe.