O painel de silicato de cálcio reforçado com fibras é fabricado a partir de fibras inorgânicas minerais ou de celulose combinadas com cálcio e sílica como principais materiais de cimentação. Estes materiais são submetidos a um processo de polpação, moldagem e, em seguida, a um processo de cura a alta temperatura e alta pressão em vapor saturado, que forma um coloide de silicato de cálcio que se solidifica em placas duráveis.
Então, como se forma exatamente o silicato de cálcio e que papel desempenham as fibras de reforço no painel? Com base na minha experiência, explicarei cada aspeto em pormenor a seguir.
Mecanismo de formação do silicato de cálcio
O silicato de cálcio é sintetizado através de uma reação hidrotérmica entre materiais de cálcio e sílica. A fonte de cálcio, tipicamente cal (CaO), inclui materiais como cal, cal apagada e escória de carboneto de cálcio. A fonte de sílica, composta principalmente por SiO₂, inclui terra de diatomáceas, pó de quartzo e cinzas volantes.
Na prática, a produção de placas de silicato de cálcio incorpora frequentemente uma pequena quantidade de cimento para melhorar a moldabilidade e o controlo. A maioria dos fabricantes utiliza atualmente uma mistura de cal e cimento, substituindo parte da cal por cimento para um melhor controlo da produção. A reação hidrotérmica do silicato de cálcio neste sistema cal-cimento é ilustrada na Fig. 1.
O mecanismo de reação do silicato de cálcio, como se mostra na Figura 2, pode ser dividido em três fases principais:
Fase de pré-cura a pressão normal: Nesta fase inicial, o cimento reage na água para formar silicato dicálcico (C₂S) e silicato tricálcico (C₃S). Em condições ambientais, o C₂S hidrata para produzir C₂SH₂, enquanto o C₃S hidrata para formar silicato de cálcio hidratado altamente alcalino (C₂SH₂) e Ca(OH)₂, embora estes compostos geralmente não reajam significativamente com o material de sílica.
Fase de cura em autoclave: À medida que a temperatura e a pressão aumentam, o material de sílica começa a dissolver-se rapidamente e reage com Ca(OH)₂ para formar silicato de cálcio hidratado altamente alcalino (C₂SH(A)), consumindo Ca(OH)₂ no processo. A temperaturas elevadas, o C₂SH (A) é instável e reage com o SiO₂ restante para se converter em silicato de cálcio hidratado de baixa alcalinidade (C₂SH (B)), formando novos cristais que crescem continuamente em cristais estáveis de tobermorita (C₅S₆H₅).
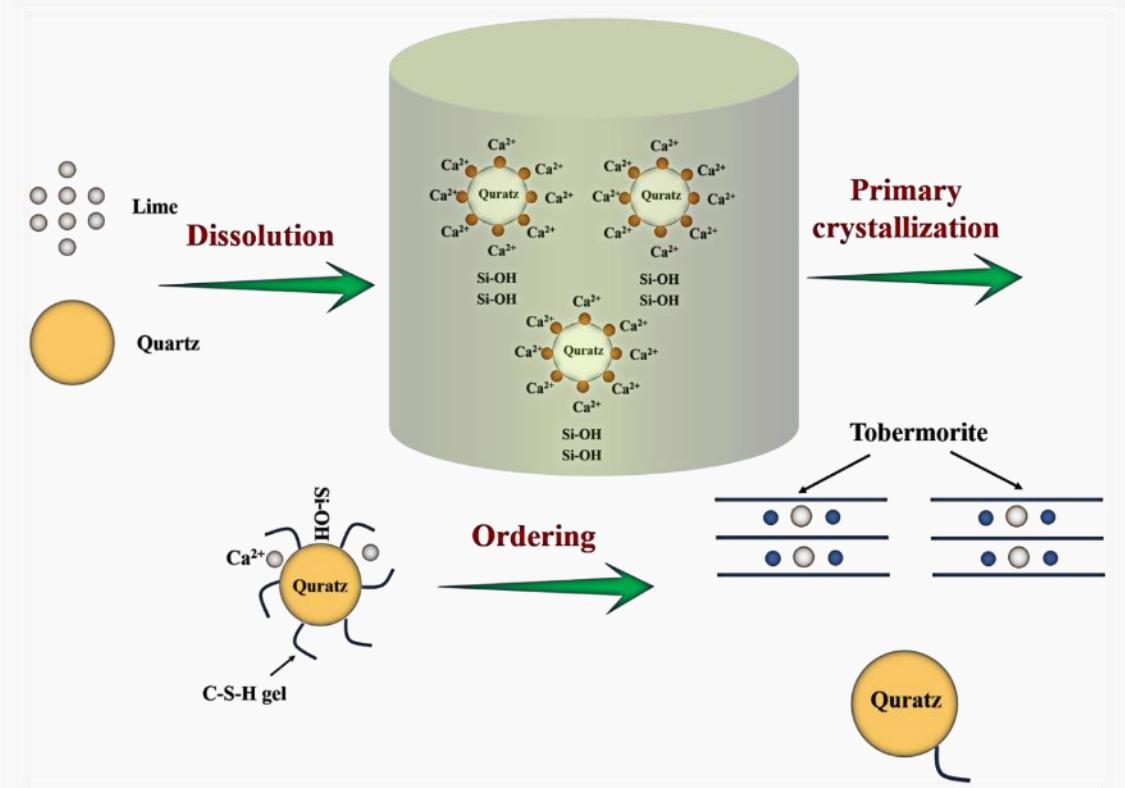
Estágio de cura prolongado: Com a cura prolongada em autoclave, os cristais de tobermorite reagem ainda mais com SiO₂ para produzir xonotlite (C₆S₆H), um silicato de cálcio duro. Em particular, devido à adição de cimento, o sistema de reação torna-se mais complexo. Na síntese hidrotérmica real, compostos como o aluminato de cálcio e o gesso da água, bem como a alumina da areia de quartzo, podem resultar num sistema de reação quaternário (CaO-SiO₂-Al₂O₃-H₂O) ou mesmo quinário (CaO-SiO₂-Al₂O₃-CaSO₄-H₂O). Consequentemente, os produtos hidrotermais finais não são apenas uma simples mistura de tobermorite e etringite, mas podem também incluir silicato de sódio e outros hidratos de silicato de cálcio contendo alumínio. No entanto, devido à estabilidade e à excelente estrutura cristalina da tobermorite, esta continua a ser o principal hidrato nas placas de silicato de cálcio, sendo permitido algum C₂SH(B) para garantir propriedades físicas e mecânicas óptimas.
Diferenças entre Tobermorite e Xonotlite
A tobermorite e a xonotlite são dois tipos principais de hidratos de silicato de cálcio com propriedades distintas. A xonotlite apresenta uma contração mínima e a maior resistência à flexão entre os materiais de silicato de cálcio, embora exija temperaturas de síntese mais elevadas e tempos de processamento mais longos em comparação com a tobermorite e a CSH(B).
Os produtos de tobermorite, normalmente sintetizados através de métodos hidrotérmicos estáticos, têm uma resistência ao calor limitada (até 650°C) e uma densidade relativamente elevada, o que os torna adequados principalmente para a indústria petroquímica.
Os produtos Xonotlite, por outro lado, são sintetizados através de métodos hidrotermais dinâmicos, o que lhes confere uma excelente resistência a altas temperaturas (até 1000°C) e baixa densidade. As fibras Xonotlite são também bio-solúveis, garantindo elevados padrões de segurança. Com estas vantagens, a xonotlite é amplamente utilizada em indústrias de alta temperatura, incluindo a metalurgia, a engenharia química e os materiais de construção. A série de placas resistentes ao fogo da FireSafe é um exemplo de placas de silicato de cálcio à base de xonotlite de alta qualidade.
O silicato de cálcio duro forma-se sob a forma de cristais prismáticos ou de agregados fibrosos alinhados paralelamente ao eixo b. Ao microscópio químico ou eletrónico, os cristais de silicato de cálcio duro sintético apresentam-se como flocos. Os cristais fibrosos têm raios de várias centenas de nanómetros e comprimentos que atingem vários milhares de nanómetros. Apesar da sua estrutura fibrosa, estes cristais não formam espaços vazios com raios da ordem das dezenas de microns; em vez disso, agregam-se em estruturas esféricas ocas. Muitos destes aglomerados atingem diâmetros de dezenas de micrómetros, formando espaços vazios com raios de 10-30 μm. Os aglomerados esféricos maiores criam cavidades internas mais substanciais e espaços mais largos entre os agregados, resultando numa densidade aparente mais baixa à medida que o diâmetro do aglomerado aumenta.
A estrutura esférica do aglomerado desempenha um papel crucial na obtenção da densidade ultra-baixa do material. Este material é normalmente formado por prensagem e secagem de uma pasta de silicato de cálcio duro. Durante o processo de filtragem-prensagem, os finos cristais fibrosos de silicato de cálcio são dispersos pelo fluxo de água, reduzindo os espaços entre os cristais e aumentando a densidade devido às forças capilares.
No entanto, quando estes cristais fibrosos formam aglomerados esféricos, o fluxo de água durante a prensagem do filtro não os consegue alinhar direcionalmente. Este facto confere aos aglomerados força suficiente para resistir à compressão excessiva. Durante a secagem, os grandes espaços entre as esferas aceleram a evaporação da água e impedem a compactação sem restrições das fibras, o que reduz as forças capilares excessivas. Isto minimiza o encolhimento e assegura que o material permanece ultra-leve.
Mecanismo e requisitos de desempenho do reforço de fibra
Os materiais fibrosos melhoram as placas de silicato de cálcio bloqueando as fissuras, endurecendo a estrutura e reduzindo a formação e a propagação de defeitos internos. O efeito de reforço depende de vários factores, incluindo o tipo de fibra, o rácio de aspeto, o tratamento de polpação, a distribuição, a orientação e a força de ligação entre as fibras e a matriz do painel.
Uma distribuição uniforme das fibras forma uma rede interligada no interior da placa, maximizando o reforço. Em contrapartida, uma distribuição desigual conduz a dois problemas: a aglomeração das fibras, que provoca inconsistências de densidade, aumenta a absorção de água e reduz a vida útil do painel; e as áreas deficientes em fibras, que são mais susceptíveis a danos provocados por forças externas, comprometendo a integridade do painel.
A orientação das fibras afecta a resistência da placa. Se as fibras estiverem dispostas direcionalmente durante a moldagem, a placa pode apresentar uma elevada disparidade de resistência entre as direcções longitudinal e transversal, reduzindo a qualidade global.
A força de ligação entre a fibra e a matriz é crucial para a durabilidade. Estudos demonstram que a interface fibra-matriz é a parte mais vulnerável da prancha. Quando as fibras se ligam fortemente à matriz, absorvem mais energia de impacto, aumentando significativamente a dureza e a resistência do painel. As fibras orientadas aleatoriamente melhoram a continuidade da placa e reduzem os defeitos internos, reforçando ainda mais a sua integridade estrutural.
Com o desenvolvimento de placas de silicato de cálcioEm 1969, a partir do ano 2000, os efeitos nocivos das fibras de amianto, tradicionalmente utilizadas como materiais de reforço, tornaram-se evidentes. Em resposta, muitos países começaram a regulamentar a utilização do amianto em 1969. Para fazer face a estes desafios, os investigadores têm vindo a explorar cada vez mais fibras de reforço alternativas, como as fibras vegetais e as fibras de vidro, que são atualmente reconhecidas como tendo as seguintes propriedades
Boa dispersão na água: As fibras devem dispersar-se bem na água, formando-se uma película de água estável na sua superfície.
Resistência à corrosão alcalina: As fibras devem resistir a soluções alcalinas com um pH de 12-14, uma vez que o processo de preparação do silicato de cálcio é altamente alcalino, o que pode corroer gravemente as fibras.
Resistência a altas temperaturas e pressões: Sob condições hidrotérmicas, as fibras devem manter a compatibilidade com a matriz, juntamente com resistência e tenacidade suficientes.
Fig.7 Fibra vegetal e fibra de vidro
Embora as fibras desempenhem um papel de reforço, existe um compromisso inerente entre o teor de fibras e o peso do produto. Um maior teor de fibras aumenta a resistência mecânica, mas também aumenta o peso do produto, reduzindo as suas propriedades de isolamento térmico. Por outro lado, um baixo teor de fibras mantém o produto ultraleve, mas compromete a sua resistência mecânica, podendo não cumprir as normas de desempenho. Para além disso, a dopagem da fibra tem impacto nos custos de produção. Assim, a determinação de um teor de fibra ótimo é crucial para equilibrar a resistência mecânica e as propriedades ultraleves dos materiais de silicato de cálcio duro.
Compreender a composição das placas de silicato de cálcio permite conhecer a sua durabilidade, resistência térmica e adaptabilidade a várias aplicações. Desde o reforço de fibras até ao controlo cuidadoso das proporções de material, cada componente desempenha um papel crucial na obtenção do desempenho desejado. Se tiver mais perguntas ou precisar de informações adicionais sobre as placas de silicato de cálcio, não hesite em contactar os especialistas em Segurança contra incêndios.